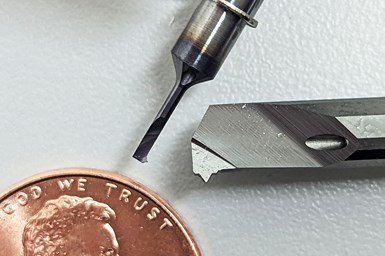
MicroBore tooling systems offer rigidity and quick-change capabilities for small-scale boring, threading, grooving and turning on Swiss-type lathes. (Photo credits: GenSwiss)
Performing boring operations on a micro level presents myriad challenges. Rigidity and position of these single-point cutters is key for what is a delicate machining process of bringing a hole to a more cylindrical diameter down its entire length.
Installing a boring bar in a Swiss-type lathe can be a challenge, especially for those in which the cutting tip is almost impossible to see let alone measure. This often requires a skilled and experienced setup person or operator which, these days, can be hard for shops to find.
Featured Content
The Utilis MicroBore system of tools and toolholders — available in the United States from GenSwiss — includes design elements to mitigate these and other issues. The MicroBore toolholder features an internal carbide stop pin to ensure repeatable boring bar position and orientation. The end of each boring bar features a precisely ground 45-degree angle that locates within 0.0004 inch against the pin. As a result, each boring bar used in the holder repeatably locates to the same position. (The operator needs only to ensure the boring bar is not installed upside down.)
A knurled nut with fine thread pitch provides force against the holder’s internal snap ring to enable the operator to insert a boring bar into the holder and tighten the nut by hand with no tools required. This prevents the chance of distorting a holder by overtightening it, while providing the simplicity to enable inexperienced operators to change or install boring bars. This type of changeover process is also helpful given the limited space inside a Swiss-type lathe’s work zone.
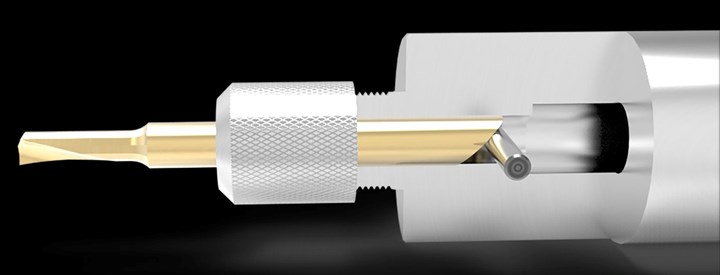
The end of each boring bar features a precisely ground 45-degree angle that locates within 0.0004 inch against the internal carbide stop pin.
Of course, the holder itself has to be oriented correctly when installed in a Swiss-type’s gang plate or dog leg such that the tool tip is in the proper radial position relative to the workpiece bore. Although each holder has a machined flat, a set screw can cause the toolholder to slightly twist as the screw is tightened. It’s largely not a big problem for relatively large tools to be a couple of degrees out of proper orientation, but it can cause significant problems for micro boring operations.
Vibration is the biggest enemy of a boring bar.
That’s why the MicroBore system includes an optional gaging plug having a precision rectangular feature on one end and the same 45-degree ground angle as the boring bars on the opposite end that is installed in the toolholder. This enables an operator to run a dial indicator over the 25-mm-wide, ground and polished plug surface to ensure it is level (meaning the holder is properly oriented). After that, the gaging plug is removed and the boring bar can be installed. This is recommended for applications in which bore holes are smaller in diameter than 1.5 mm.
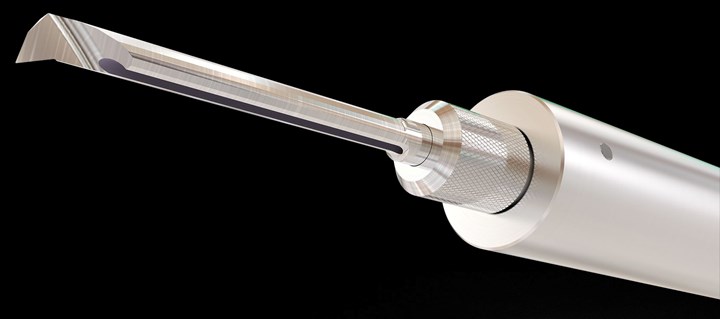
This cutaway of a boring bar shows an internal coolant channel that is common to all MicroBore tooling systems.
All MicroBore toolholders and boring bars also have through-tool coolant capability. The coolant kits (rated to 3,000 psi) feature a range of plumbing lines and fittings and accessories to enable installation on many different Swiss-type lathes and toolholding systems.
Every boring bar also features facets down the tool’s neck, each having different widths, which minimizes the chance for harmonics to develop during machining. This enables the boring bars to offer rigidity even if they are long and have small diameters. The MicroBore ID-work system includes geometries for conventional boring (down to 0.016 inch), threading (as small as M1 thread size), turning, grooving and more.
RELATED CONTENT
-
Advantages of Cellular Manufacturing
Manufacturing cells are used to minimize product movement as well as materials, equipment and labor during the manufacturing process. By reducing cycle times and material handling, these cells help shops more easily meet customer demands regarding cost, quality and leadtimes.
-
Cutting Tool Coating Production
This article looks at the coating methods available for carbide cutting tools.
-
The Many Sides of Workholding
Here's a broad look at different ways to approach workholding, from bar feeders to collet chucks to robotics.