Rotary Transfer Technology Becoming More Flexible
This rotary transfer machine platform, which enables shops to reconfigure equipment to change over to new jobs as needed, is said to be effective for batch sizes of only 50 parts.
#techbrief
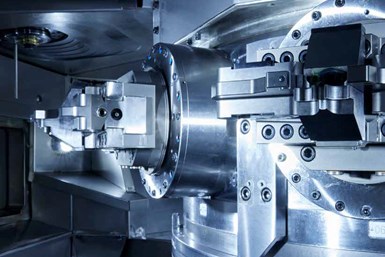
For this rotary transfer machine platform, a zero-point clamping system is said to ensure positioning repeatability for exchanging machining units at any given station. Photo Credit: Mikron
Manufacturers of traditional high-volume turning and milling equipment continue to incorporate flexibility into their machine designs to enable shops to effectively run jobs in smaller batch sizes.
One example is the MultiX rotary transfer platform from Mikron featuring configurable (and then reconfigurable) machines that the company says can accommodate production runs of 50 to 5 million parts.
Featured Content
The concept enables near à la carte configuration, depending on a shop’s current and future needs. For example, users select machine base; transfer tables with 4 to 24 stations; exchangeable machining units (three machining units can operate simultaneously at each station); workpiece clamping and positioning systems, including those for B-C axes movement; spindles (electro spindles; double spindles; U-axis spindles; and so on), automatic toolchanger-style (spindle with four tools, disk with 12 tools or upper and lower disk each with 12 tools); and loading/unloading system (such as standard three-axis pick-and-place and six-axis robot).
Three machining units can operate simultaneously at each station.
The machining units differ in size, number of axes, strokes and size of compatible spindles. They can be exchanged within the platform and reused in different configurations. A zero-point clamping system is said to ensure positioning repeatability for machining units at any given station. According to the company, not only does this offer process flexibility but scalability to add or replace machining functionality as needed.
The operating software and human-machine interface (HMI) is said to be intuitive as well as adaptable to new machine configurations. The software also offers capabilities such as production scheduling, component temperature monitoring and statistical process control (SPC) monitoring.
RELATED CONTENT
-
Rotary Transfer: Turning Up the Volume
This contract manufacturer set its sights on high volume, precision turning and assembly of complex components from Day 1 and continues to succeed in a market many have abandoned using CNC rotary transfer machining.
-
Captive Shop Must Still Compete
Often, a captive shop seems to have it made by job shop standards. In the case of this division of ITW Welding, “work is not given, it’s earned.”
-
Rotary Transfer Offers Full OD Turning Between Centers
This small-footprint trunnion rotary transfer machine includes an isolated cell to perform full OD turning between centers for improved concentricity compared to flipping parts in a station for backside turning or moving the part to another clamping position.