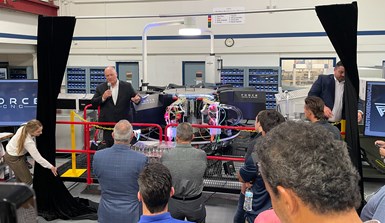
Hydromat President Matthias Walter introduced the new Force CNC rotary transfer machine at the company’s recent Oktoberfest open house at its St. Louis headquarters. (Photo credits: PM)
Hydromat’s Force CNC rotary transfer machine features a ballscrew electromechanical system said to offer modularity with options for one- through four-axis tool spindle configurations, providing turning, drilling, tapping, threading, thread milling, single-point threading, profiling and milling capabilities.
The Force machine can be fitted with 12 or 16 horizontal machining stations and six or eight vertical machining stations, with a maximum spindle speed of 8,500 rpm for mill/drill units and 5,000 rpm for turning. The machine comes equipped with Force 50/150 tool spindle units, which are FANUC-controlled and offer technology for artificial intelligence learning and chipbreaking functions. The units come standard with a C-axis servomotor for tapping or single-point turning compatibility, as well as direct-coupled motor/ballscrew for the Y and Z axes.
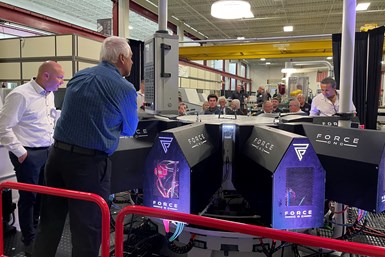
Force ballscrew electromechanical tooling units are said to provide high rigidity, flexibility and accuracy for various precision-machining applications.
The standard tool spindle unit offers Z-axis motion. The two-axis unit features X- and Z-axis movement. The three-axis unit’s Z axis includes an X- and Y-axis cross slide. The four-axis unit, which enables boring and eccentric turning operations, has a two-axis lathe unit with two-axis cross slide for X-, Y-, Z- and U-axis motion. All axes are direct-drive sans the X axis, which is belt-driven. Tooling units can be retrofitted to the company’s existing Epic CNC machines and legacy hydraulic machines with FANUC RS package.
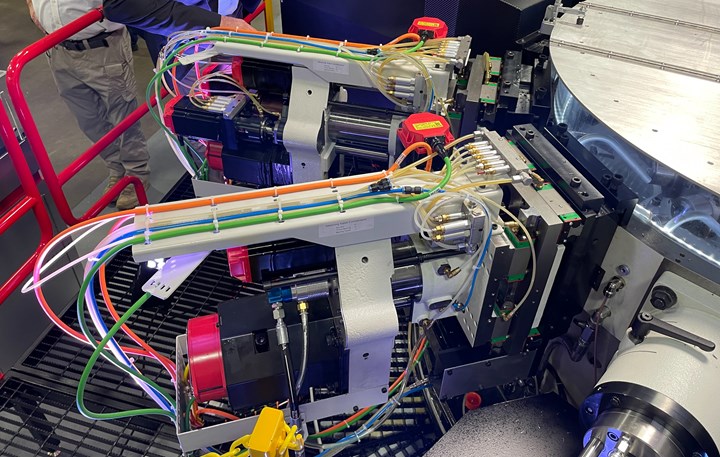
Tool spindle units are available in one-, two-, three- and four-axis configurations.
The Force is equipped with a FANUC 30i Model B CNC, which offers an intuitive and easy-to-use interface that caters to both programmers and on-site operators, the company says. The control features a high-speed processing capability, enabling faster cycle times and improved productivity. It also has advanced diagnostic and maintenance features, enabling easy troubleshooting and maintenance. (Hydromat is part of the FANUC America Authorized CNC System Integrator network.)
The company says the machine offers higher rigidity due in part to a larger HSK 50 tool holder (compared to HSK 40) and bigger 50-mm bearing tool-spindle design. Maximum part length is 6 inches in stock sizes to 1.75 inches (round), 1.5 inches (hex) and 1.25 inches (square).
RELATED CONTENT
-
Rotary Transfer: Turning Up the Volume
This contract manufacturer set its sights on high volume, precision turning and assembly of complex components from Day 1 and continues to succeed in a market many have abandoned using CNC rotary transfer machining.
-
Rotary Transfer Offers Full OD Turning Between Centers
This small-footprint trunnion rotary transfer machine includes an isolated cell to perform full OD turning between centers for improved concentricity compared to flipping parts in a station for backside turning or moving the part to another clamping position.
-
Precision Machining Technology Moving Shops Forward
New equipment and software continue to be developed to support the needs of production machine shops like yours. Here’s a sample of technology now on the market that can help you grow your operation and become more efficient.