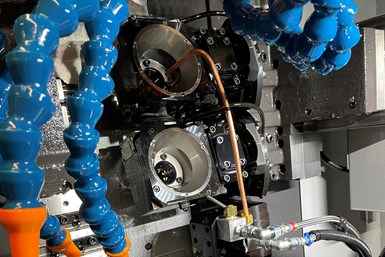
The complex geometry of bone screw threads is such that, while possible, conventional operations such as single-point threading can be tricky and time consuming. Multiple tool passes are required and, because the thread profiles are commonly deep, chatter can be an issue. That’s why shops sometimes opt for thread whirling, which is more akin to a milling operation using multiple cutting edges in a cutter body rotating around the part which create threads in one pass, offering higher metal removal rates and better finishes.
However, some modern bone screw designs have two thread leads as this enables faster, more controlled screw insertion. Traditionally, these screws might be machined with two single-point threading operations or one thread whirling operation followed by a subsequent single-point operation.
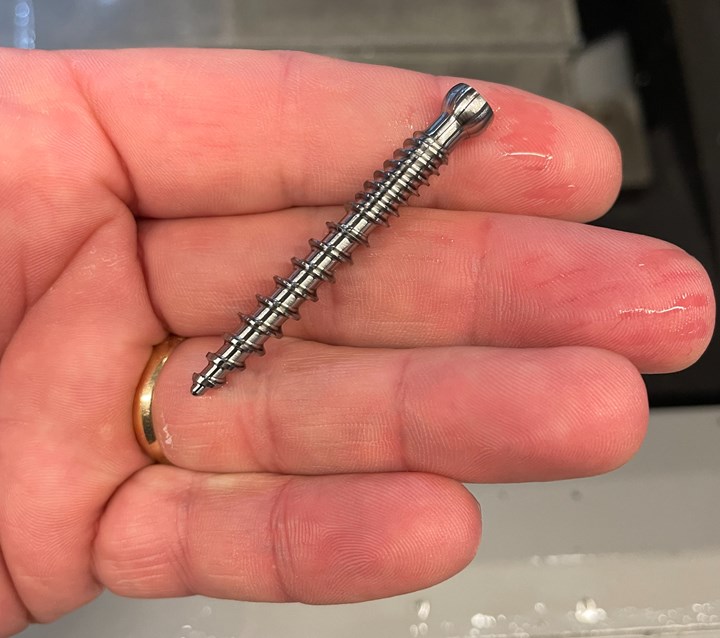
Tsugami/Rem Sales offers an alternate option on its S206-II Swiss-type CNC lathes that offers the room to be fitted with two thread whirling attachments. That way, both thread leads can be created in one setup, eliminating a second single-point threading operation to speed overall manufacturing time.
The company performed a machining test of a dual-lead bone screw made from 303 stainless steel on a S206-II with dual thread whirling attachments. Cycle time for each screw was 4.79 minutes, which would produce 85 screws per 8-hour shift.
RELATED CONTENT
-
Selecting the Right Milling Tool for Any Machining Task
High-performance milling cutters combine high cutting data with long tool life and efficiency, but certain factors must be considered when selecting tools for different machining tasks.
-
Tools and Technologies for Deep Hole Drilling
Understanding the challenges of deep hole drilling and knowing how to select and apply the appropriate tools will help a shop profit from this operation.
-
When Thread Milling Makes Sense
Threading a workpiece is a fundamental metalworking process that every manufacturing engineer takes for granted.