Rollomatic Grinding Machines for Firearm, Ammunition Industry
Appears in Print as: 'Grinding Machines for Firearm, Ammo Industry'
The GrindSmart 630XW 6‐axis tool grinding machine and the ShapeSmart NP50 5‐axis pinch/peel cylindrical grinding machine offer custom-made tooling for manufacturing parts for the weapons industry.
Edited by Angela Osborne
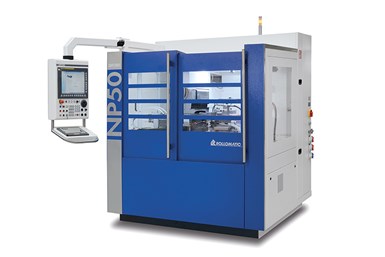
Rollomatic’s ShapeSmart NP50 5‐axis pinch/peel cylindrical grinding machine.
Rollomatic offers two grinding machines that have specific capabilities for grinding a variety of gun‐related tooling and components — the GrindSmart 630XW 6‐axis tool grinding machine and the ShapeSmart NP50 5‐axis pinch/peel cylindrical grinding machine. The company has worked with manufacturers in the firearms and ammunition industries to develop and fine‐tune these machines to provide custom-made grinding processes for a variety of fields.
The machines are well suited for the production grinding of firing pins and prototyping cylindrical parts for guns, as well as rifle chamber manufacturing and reconditioning such as chamber reamers in tungsten carbide for rifle chamber cutting.
The GrindSmart 630XW 6‐axis tool grinding machine comes with a 6‐station wheel and nozzle changer; automatic tool loader/unloader; linear motion technology for improved surface finish; and a universal workhead with high‐speed capability to combine high‐accuracy cylindrical grinding and geometry grinding. It also offers a variety of workholding and toolholding solutions, including custom‐made fixtures. Laser measuring is also included.
The ShapeSmart NP50 5‐axis pinch/peel cylindrical grinding machine features an automatic 3‐axis tool loader/unloader; and a pinch/peel grinding process in combination with V‐block part support and with simultaneous grinding of roughing and finishing passes. It offers multipass grinding for efficient heavy stock removal; a diameter range from 0.0008" to 1"; and non‐round pinch/peel grinding for all non‐round shapes such as square, rectangle, oval, corner radius and any other non‐round profile. An onboard diameter gauge is also included.
RELATED CONTENT
-
Using Grinding Versus EDM to Finish Form Tools
Finishing carbide inserts using EDM or grinding.
-
Bond Selection for Production Grinding
Proper grinding wheel selection is essential to ensure that the required part quality, production rate, and overall cost per part is achieved. Although the type of abrasive grain is often a primary driver of wheel selection, the bonding type can also play a key role in optimizing a grinding operation.
-
Rethinking the Grinding Cycle to Optimize Abrasives Cost Savings
For cost savings in grinding, the complete process should be examined, looking for a comprehensive solution using the latest technologies.