Vertical Machining Center Designed for Flexibility
IMTS 2022: Hardinge’s Bridgeport XR1000 VMC is said to be well suited for machining everything from simple workpieces and quality molds/dies to complex prismatic parts.
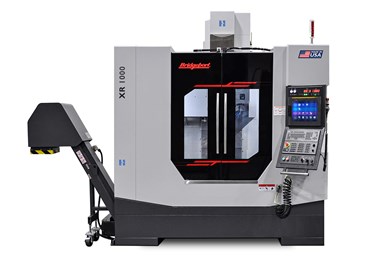
Photo Credit: Hardinge
Hardinge’s Bridgeport XR1000 VMC is said to be well suited for machining everything from simple workpieces and quality molds/dies to complex prismatic parts. It boasts the latest FANUC Plus control system with a high-resolution 15" touch screen and features the Intelligent Human Machine Interface (iHMI) which is designed to increase ease-of-use, improve operational efficiency and bring more control to the shop floor.
Some of the standard features of the Bridgeport XR1000 include 12K Air Oil direct drive spindle, Big Plus CAT 40, 12,000-rpm spindle speed, CT40 or BT40 taper spindles, Big-Plus face taper spindle, a high-retention draw bar, rigid tapping and thermal compensation.
Benefits of the redesigned XR1000 include shorter lead times, improved user experience levels and a greater ability for full turnkey offerings for Hardinge’s customers.
RELATED CONTENT
-
Selecting A VMC: Factors To Consider
A three-, four- or five-axis vertical machining center can run the gamut of capability and cost. Assessing your application requirements now and in the future can make for a much wiser machining center purchase.
-
Human-Like Robot Automates Secondary Machining Operations
Two seven-axis robots enable two second-op mills to run lights out eight hours in the evenings to win 64 hours of unattended machining time per week for this Ventura, California, shop.
-
Automatically Optimize Your CNC Machining Feed Rates
New feed-rate-optimization technology can enable CAM programmers to reduce cycle times and increase tool life for milling and turning operations.