SW’s Single-Table Machines Designed for Machining Large Parts
Appears in Print as: 'Single-Table Machines Designed for Machining Large Parts'
SW’s BA W08-11 and BA W08-21 can be automated with a variety of solutions, including TopRob which facilitates the loading and unloading of large and heavy workpieces with the aid of robots on platforms or gantries above the machine.
Edited by Angela Osborne
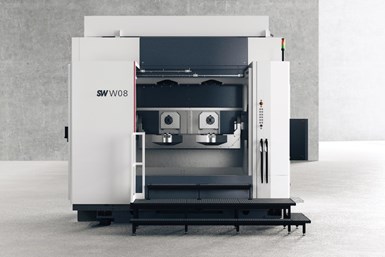
SW’s BA W08-11 was developed for machining aluminum workpieces.
SW’s two newest single-table machines, the BA W08-11 and BA W08-21, are designed for the precise machining of large workpieces with long cycle times. With one worktable and one or two spindles, these machines have large working areas enabling the high-performance machining of especially large workpieces, including battery trays, turbine blades, gearbox housings, steering knuckles and subframes.
SW’s BA W08-11 was developed for machining aluminum workpieces. The use of linear direct drives enables the machine to have an acceleration of 2 g in the linear axes. It has a 35-kW spindle with up to 17,000 rpm at 80 Nm and HSK-A63 interface. HSK-A80 and HSK-A100 spindles are also available.
The BA W08-11 prototype has a working range of 1,500 mm (X), 1,025 mm (Y) and 660 mm (Z). The interference zone of the A-axis has a diameter of 1,650 mm and a length of 1,830 mm. A space version features a larger interference zone diameter of 1,850 mm and length of 1,980 mm on the A-axis.
SW also developed the BA W08-21, a twin-spindle sister model that enables machining of two workpieces at the same time. In this machine, travel of the spindles is 800 mm (X), 1,025 mm (Y) and 660 mm (Z). These specifications apply to the HSK-A63 and HSK-A80 interfaces. In addition to single-table machines with linear direct drives for the machining of non-magnetic materials, SW is also developing single-table machines with proven ball screw drives for the machining of conventional iron, steel or nickel-based materials.
The new models in the BA W08 series can be automated with a variety of solutions, including TopRob which facilitates the loading and unloading of large and heavy workpieces with the aid of robots on platforms or gantries above the machine. Multiple grippers enable the rapid exchange of finished and raw parts. Another option is to load and unload the machines from the front with an SW FloorRob.
RELATED CONTENT
-
Turning Machines Help Firearms Supplier Achieve Rapid Growth
Working closely with its machine tool supplier, this firearms manufacturer has quickly expanded its lineup of turning machines to deliver quality products and faster delivery.
-
Burr-Free Micro Thread Whirling
Threading is usually the last operation when machining components, which is why the process needs to be reliable and highly precise. DC Swiss has developed an internal thread whirler, which leaves micro threads burr-free, even in demanding, hard-to-machine materials.
-
Shop Evolves with CNC Turning
Debbie Sommers answered a newspaper ad for a receptionist job at a South Elgin, Illinois, screw machine shop in 1980. Today, she owns the shop, an 18,000-square-foot facility with 20 employees and sales growth of 25 percent in 2017.