Getting More Production From Swiss Turning Centers
Buying a new CNC Swiss turning center is a substantial investment. For the best return, look closely for capabilities that enable the best utilization of the machine.
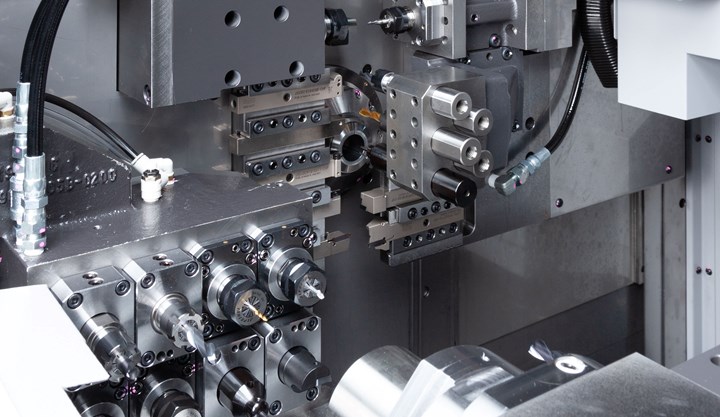
Tsugami BW329Z 32 mm 9-axis Swiss Turning Center
So you’re thinking about buying a new CNC Swiss turning center. Comparing specs is fine as far as that goes, but what you really want is a machine that provides the best return on investment. That analysis goes beyond the machine itself. How many hours a day can you run it? How easy is it to program? How quickly can it be set up? How forgiving is it with less-than-perfect bar stock?
These and other factors will make the difference between an adequate investment and a spectacular one.
Tsugami has been making CNC Swiss-style lathes for 50+ years, and their engineering team has vast experience with both the equipment and the process. Here are four key factors they suggest considering for the best payback from your Swiss turning center.
Dealing With Chips
A perennial problem with Swiss turning is the forming of long stringy chips that quickly weave themselves into bird’s nests, requiring frequent operator intervention to clear the machine. This demands constant monitoring and essentially rules out the ability to run unattended. It increases labor costs and reduces the daily output of a Swiss turning center.
Oscillation cutting rapidly moves the tool in and out of the cut to eliminate formation of long stringy chips.
Cutting tool manufacturers have been working to develop better tool geometries for Swiss turning, but the problem remains with many materials where chip breaking is a persistent problem. A relatively new technology that puts an end to long chip formation is oscillation cutting. The basic idea of this process is to continually feed the tool edge into the cut, then retract slightly, and feed again to create a moment of air cutting so that very short chips are generated that fall harmlessly into the chip conveyor below. This axis feed motion is synchronized with the spindle rotation which ensures repeatable and extremely predictable chip-breaking action. In addition to eliminating the chip buildup problem, the interrupted cut reduces heat concentrated at the cutting area.
The oscillation in and out of the cut happens so rapidly it is impossible to see with the naked eye. A typical oscillation rate, for example, is 1.5 cycles per 360° of spindle rotation which creates a harmonic frequency < 50Hz. In addition to OD turning operations, oscillation cutting can be used for drilling, boring, grooving and cutoff. Standard canned cycles can be used with oscillation cutting as well.
A great aspect of oscillation cutting is the wide range of materials on which it is effective. You’d expect it to work with softer, stringy metals but it also can be used with hard, difficult-to-cut materials such as aerospace alloys where reduced heat generation is also a major benefit.
By eliminating the need to constantly monitor for chip buildup, oscillation cutting finally unlocks the door to unattended machining, enabling shops to run their machines more hours per day and with fewer maintenance interruptions. Oscillation cutting is easy to program (activated with a single G code). To accelerate the learning process, Tsugami engineers have extensive experience with a wide range of materials and can help users more quickly achieve optimum process parameters.
Faster Part Programming
To run complex machines such as multi-axis Swiss turning centers, you must pay keen attention to CNC part programming. The worst thing that can happen is having an expensive machine sitting idle because you can’t program it, which was an all-to-common occurrence in the early days of multitasking technology. Even today, with multiple processes happening concurrently, there is a significant risk of collisions that can break tools or cause damage to the machine. But being excessively cautious can lead to inflated cycle times that rob you of the total throughput made possible by multitasking machining.
Tsugami addresses this issue with its Abile programming system that comes free with nearly every Tsugami machine model. Capable of programming moderately complex parts, the software is designed to get new users up and running quickly. Tsugami says that with just a half day of training, new programmers (to Swiss) can begin generating 2 or 3 path (channel) programs.
A very nice aspect of Abile software is that a version is written for each Tsugami machine type so that unique post processors are not required, which is a common point of contention when working with third-party software. Abile incorporates all basic machining features, and most material types, with predetermined speed and feed rates. It automatically checks for interference problems to enable the creation of more efficient and safe part programs, and in less time.
Reducing Setup Time
Switching out tools isn’t hard, but it does take time, particularly in precision Swiss work where new tools are often touched off manually to precisely establish tool tip location. Quick change toolholders can certainly help, and several very good systems are available. But a quick-change tool connection only addresses half the changeover issue. Establishing new tool offset data manually takes more time and can be a source of costly mistakes. The key to making the most of quick-change tooling is to pair it with a tool presetter so that tool offset data can be established offline and entered in seconds.
As well as accommodating several third-party systems, Tsugami has its own quick-change system that cuts tool change time down to 30 seconds or less. It only requires loosening a single screw to remove a toolholder. Plus, presetting tool length minimizes operator error during touch-off and can eliminate that task altogether on all but the highest tolerance parts. These attachments fit nearly every current Tsugami model, as well as some previous models. These quick-change units are all ground mating surfaces with repeatability of .01µm so accuracy is no issue.
More Forgiving Workholding
A hard lesson many shops have learned since Covid is that the cost and availability of high-quality barstock are always in question. This has led many Swiss shops to increase use of unground barstock which can have significant surface imperfections and much looser tolerances on the roundness and straightness of the bar.
Tsugami America is addressing this issue with its SmartFlex Guide Bushing System which is designed to create consistent support when machining less-than-favorable quality bar stock. It can also improve roundness after machining by providing even pressure around the bar at all times. This guide bushing system is created by converting the standard Tsugami direct drive guide bushing internals with a pneumatic draw tube assembly made by JBS.
With the ability to compensate for as much as 0.012” of barstock variation, SmartFlex alleviates the need for ground bar stock in most applications. It’s relatively easy to install and adjust, and provides better axial support for the bar. This system also allows for regrips to be performed on longer parts without the need to use the subspindle for support, using the high-pressure clamping function.
Tsugami has tested the bushing on a wide range of materials. In one case, the raw material was 1” extruded 6061 aluminum with initial roundness of 0.0014”. After a 1.5” long OD turning cut at 0.185” depth of cut, the finished part was machined to a roundness value of 0.00015”.
Get Help From People Who Understand Swiss Turning
With so many more shops now taking on Swiss turning, it helps to have experts to help with applications support, training, and automated process development. With over 250 staff years of experience, Tsugami America engineers enjoy the challenge of helping shops produce superior Swiss parts faster and for less.
Moreover, with the process enhancements mentioned here as well as many others, unattended or full lights-out machining is finally within reach with Swiss turning. Tsugami engineers can help you flip the switch. They can also provide guidance to reduce set-up time, scrap rates, and slash changeover times.
For more information, please visit the Tsugami America website.