
Innovative Controls’ in-house manufacturing capabilities enable it to design, assemble and ship assemblies —such as these gage bezels for fire trucks — faster than outsourcing those capabilities.
Innovative Controls’ efforts to become vertically integrated with its manufacturing capabilities started with digital silk screening, but creating its own machine shop — which includes a CNC Swiss-type lathe — soon followed.
After working in industrial sales for a number of years, Mike Michna, Innovative Controls’ president, sought other avenues to create a company offering a manufacturing niche. In the late 80s, he recognized that the pump panels on fire trucks were not user friendly in terms of function or layout for firefighters to efficiently control and operate at a stressful scene of a fire.
Featured Content
The Pittsburgh, Pennsylvania, company — which now occupies multiple bays inside a huge, former Westinghouse turbine manufacturing facility — has since grown to become the market leader of pump panel control, diagnostic and identification products for fire apparatus OEMs. It designs, manufactures and distributes devices, including tank level monitors, valve control assemblies, pressure gauges, product identification bezels, safety message bezels, associated graphics and plumbing products for those vehicles. Innovative Controls also offers contract manufacturing services for other industries such as medical.
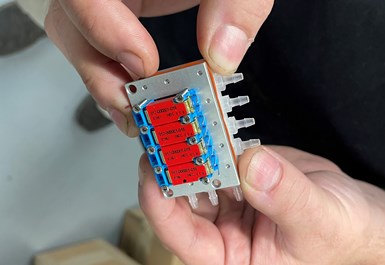
The company’s goal as a contract manufacturer is to take on business only if it is going to be providing assemblies, such as this medical air module.
Michna says the goal is not to provide individual parts to customers, but rather complete assemblies. Having virtually all requisite machining and manufacturing capabilities in-house (the company still outsources die casting and injection molding) has enabled the company to manufacture those assemblies more cost effectively and at a higher quality while being able to respond faster to customer needs as it has control over all those processes.
Starting with Silk Screening
Innovative Controls is perhaps the most capable operation I’ve visited in terms of its in-house manufacturing capabilities, although high-volume injection molding and die casting for components such as custom bezels with recesses for color coding and identification are outsourced. Michna says the company has taken a “we’ll figure it out” approach to adding new technology, leaning on industry experts along the way. Digital silk screening was the initial technology it sought to figure out.
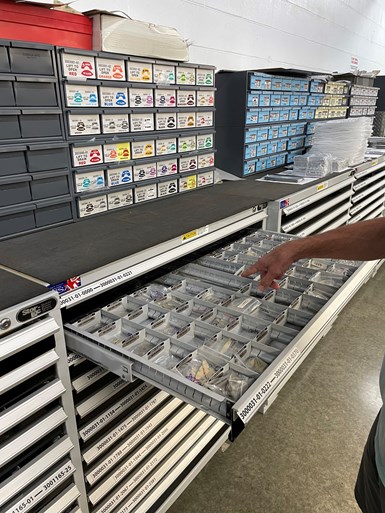
Digital silk screening was the first capability Innovative Controls brought in house.
Michna notes that early pump panel components used low-grade plastic and paint or vinyl labels for component identification and instructions that would fade or peel over time. He found that polycarbonates used on gasoline pumps were better resistant to UV light and offer longer life. The company initially used conventional silk screening technology (think squeegees) to color and code labels one at a time. It then brought in digital silk screening equipment to print in higher volumes with more flexibility. The trick was learning how to get the ink to stick to the polycarbonate material. To effectively do this requires precise control of humidity and static electricity in the room in which the (now two) digital silk screening machines are located. Having this capability in-house enables the company to design, print and ship labels in 24 hours.
The goal is to provide assemblies to customers, not just individual components.
The company has since added a wealth of other processes. This includes CNC knife cutting and panel routing; polydoming; automated circuit board assembly; and mechanical and electrical assembly. The latest piece of equipment is a Trumpf TruPunch punch press, which was added with the goal of creating a full fabrication and paint shop for sheet metal components such as cabinets.
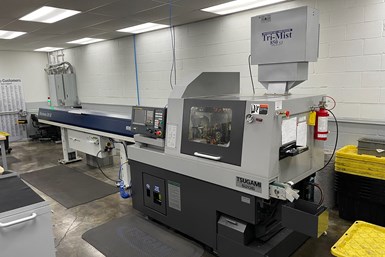
Machinist Matthew Resnick was able to get this Swiss-type lathe up and running again. Its first production job was a 500,000-piece run for a medical component.
But CNC machining is also a key capability the company continues to grow which it previously outsourced. For example, years ago, it used a vendor in Minnesota to machine a small medical component called a barb for an assembly. Although the vendor’s price was good, it wasn’t as competitive as Michna would have liked. As a result, Innovative Controls jumped in with both feet, purchasing a Tsugami S206 Swiss-type lathe with barfeeder, its first CNC machine tool. Having no machinists on staff, the company initially hired a subcontractor to run jobs on that machine every once in a while. Michna admits the company didn’t really understand Swiss-type machining well, and initially didn’t leverage the capabilities such a platform offers, especially for high-volume production.
Therefore, in early 2020, Innovative Controls hired machinist Matthew Resnick to establish a more formal in-house machine shop. Resnick suggested adding a CNC chucker lathe and small VMC, which the company in fact had already ordered. These were also Tsugami models: an MQBSY-II lathe with FMB barfeeder and VA2 high-speed mill (the company has since added a second VA2).
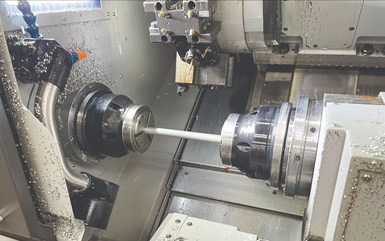
The chucker lathe primarily machines a family of extrusions used to create push/pull handles.
While waiting for delivery of that equipment, Resnick had a couple months to get the Swiss-type up and running again. He says the machine basically required a good cleaning, and he started to learn Abile, the free CAM programming software Tsugami offers for its Swiss-types. Innovative Controls also added a Firetrace fire suppression system to the machine to provide the confidence to run it lights out. Over a span of three months, the machine was able to complete a 500,000-piece production run for the medical component with only a few minor tweaks required, Resnick notes. The original cycle time was 14 seconds per part using three tools, but he reduced that to 9 seconds by replacing two tools with one custom form tool that also created more manageable chips.
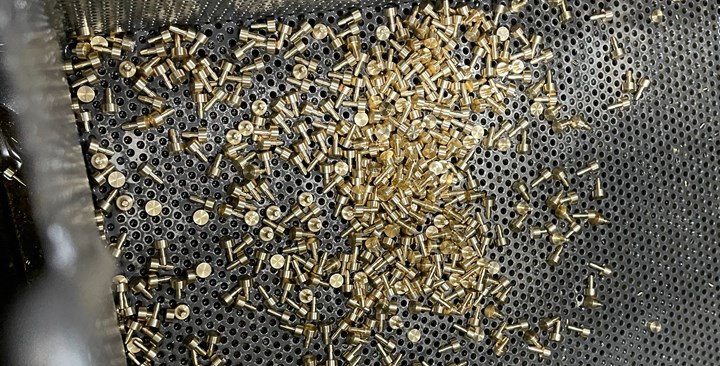
Cycle time for these medical components produced on the Swiss-type have been reduced from 14 seconds to 9 seconds per part after replacing two tools with a custom form tool.
The chucker is primarily used to run a family of aluminum extrusion rods of various lengths that are assembled to create push/pull handles used on fire truck pump panels. A collaborative robot from Universal Robots (integrated by ProCobots) was recently added to enable long stretches of unattended operation. As shown in the video below, completed parts are pushed through the subspindle for the cobot to grab and transfer to trays. Once a tray is full of completed parts, the cobot tops it with an empty tray it then will begin loading. Stacks of trays can then be easily boxed and sent for anodizing.
The VA2 mills are used to create a variety of parts, including plates for a medical assembly and molds the company uses to pot electronics to protect against vibration and moisture. These machines feature 35,000-rpm spindles, quick-change tooling plates from Saunders Machine Works, Renishaw touch probes and Metrol tool breakage detectors that can also measure tools. Being that Resnick runs the machine shop on his own, these types of devices make it easy for someone else to run a job if he’s not available.
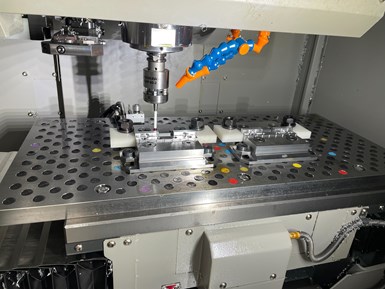
Innovative Controls makes maximum use of the available work envelope of its high-speed mills using quick-change fixturing that speed change-overs.
A Second Swiss-Type?
Similarly, Innovative Controls finds value having this (for now) four-machine shop beyond improved customer responsiveness. Resnick is able to respond faster to its designers’ needs as well as consult with them to offer suggestions to revise designs, loosen tolerances, etc., to speed, simplify or reduce the cost of machining parts for the company’s new products.
In terms of machining technology, Innovative Controls might add a second Swiss-type if demand for medical parts increases. Michna says that while he doesn’t know where the fire apparatus industry is headed, those vehicles will always require storage cabinets, accurate pump control and effective communication of the pumping system with the engine’s computer. In that respect, the company remains set up for future success in that industry while its substantial manufacturing competency in many areas offers the potential to grow the business in many other industries. Michna says the key is to never fall behind in technology and be bold enough to invest in it, learn it and continue to find ways to be more effective using it.
RELATED CONTENT
-
Swiss-Type Machines: More Than Just a Lathe
CNC Swiss-Type machines have more capability built in than ever before. Many of these capabilites can be accessed using attachments that increase the throughput of the machine tool, improve the quality of the work coming off the machine and reduce or eliminate the need for secondary operations even for very complex workpieces.
-
Advancements in Thread Whirling Tooling Technology
Many understand the advantages of thread whirling on a CNC Swiss-type. However, new tooling technology for this thread-machining process can further improve cycle times and reduce cost per part.
-
Moving Up To CNC Swiss Screw Machines
Three new CNC Swiss machines in 18 months have provided real growth for this Illinois shop.