Ultrasonic Additive Manufacturing (UAM) Cooperates with Other Processes
Fabrisonic showcases UAM paired with conventional and other additive processes in Booth 433017.
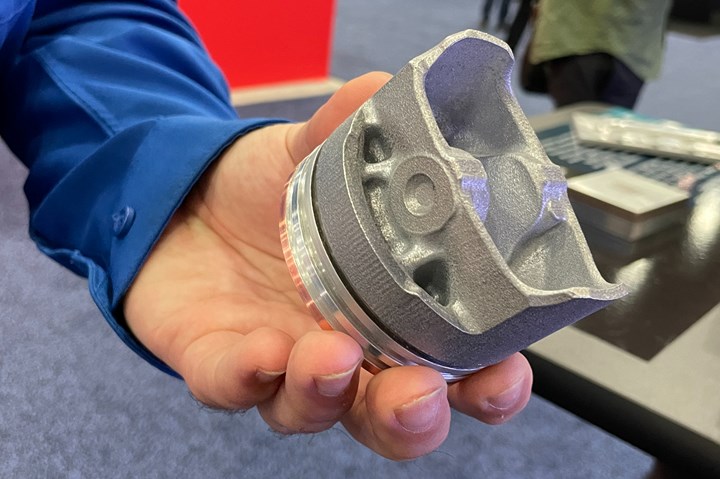
This piston features a copper and stainless steel UAM 3D printed base; laser powder bed fusion was used to build the more intricate features on top. See this and other examples of ultrasonic additive manufacturing in Booth 433017.
The term “hybrid manufacturing” has generally come to mean “additive manufacturing paired with machining in the same machine,” but that definition might be too narrow. From Fabrisonic’s perspective, AM can be combined with other manufacturing processes in many ways, and the company’s booth in this year’s Additive Manufacturing Pavilion illustrates several potential applications.
Fabrisonic provides and produces parts with ultrasonic additive manufacturing (UAM) technology. UAM vibrates very thin sheets of metal together until they fuse, allowing for dissimilar metals to be combined and layered. The process generates very little heat, making it possible to embed electronics, fiber optics, sensors and other components inside these prints.
Parts on display in the booth illustrate how ultrasonic additive manufacturing can be used in combination with other processes to provide specific benefits. A conventional piece of sheet metal with a UAM rib shows one way the process can augment off-the-shelf materials — in this case, adding strength to a thin sheet just where needed, essentially creating a tailor-welded blank through an automated process. UAM can even be combined with other 3D printing processes; the engine piston shown here features a UAM base with layers of stainless steel and copper (for cooling) that was then used as a build plate so that laser powder bed fusion could add the more detailed features on top.
RELATED CONTENT
-
Customizable CNC Machine, Automation Solutions
IMTS 2022: BA W08-12 is designed for machining large workpieces made of aluminum and other nonferrous materials.
-
Starrett's Multisensor Vision System Provides Large Field of View
IMTS 2022: The AVR-FOV 0.14X multisensor vision system is designed to provide accurate, efficient measurements fora wide range of parts.
-
Horn Carbide Grades for High-Feed Milling
IMTS 2022: The SC6A and IG6B grades complement the tool system for high-feed milling and enable customers to choose the grades best adapted to their machining applications.