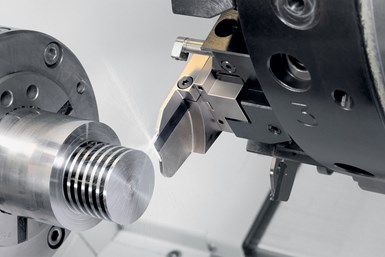
For parting-off and grooving operations, feed rate and cutting speed are important to consider as are the type of grooving tool and holder. (Photo credits: Arno Werkzeuge)
Parting off and grooving are among the most important turning operations, but they also can be demanding because there are many parameters that determine process effectiveness and production.
In addition to the rigidity of the machine, feed rate and cutting speed, the parting-off and grooving tool and its holder are decisive factors governing the quality of the operations and workpiece. Shops that don’t consider the diversity of cutting materials, blades and holders will realize these processes can become very costly. It pays to mind the advice of manufacturers of these tools such as Germany’s Arno Werkzeuge which has many years of application expertise.
Featured Content
Parting off is similar to many other turning processes as the devil is in the details. Plus, this operation plays a decisive role at the end of the turning process, after which much value has already been added to the workpiece by the time parting off operations are performed. In addition to feed rate and cutting speed, groove width and cutting depth as well as chip evacuation are factors that require particular attention.
Parting off operations play a decisive role at the end of the turning process, after which much value has already been added to the workpiece.
For example, Arno Werkzeuge offers its double-edged SA grooving system with groove widths of 1.5 to 10 mm which is suitable for parting off and grooving at cutting depths of up to 140 mm in diameter. Together with many modules, holders (including machine-related flange mounted holders) and blades, this parting-off tool is always optimally adapted to the situation.
Users can choose from six geometries, seven coatings and two solid carbide substrates for various workpiece materials. The SA grooving system is adapted to steel, stainless steel, aluminum or materials that can be difficult to machine. It is said to ensure an uninterrupted cut for applications that require optimum chipbreaking geometry, thanks to its negative chamfer geometry. This is important because chips tend to build up and jam in the groove, especially while parting off. It is also said to produce quality parting-off surfaces because the system works with low vibrations due to its high stability regardless of the feed rate and cutting speed.
For grooving applications and Swiss-type machining, the company suggests using its SE groove-turning system which offers a flexible solution because it maintains stability despite high lateral forces. The SE system enables users to part off even if workpieces have a large radius. This is shown by groove widths of 2 to 6 mm and cutting depths of 12 to 21 mm. Here, too, seven geometries are available to accommodate a range of workpiece materials. Users can also order precision-ground inserts for SA and SE systems with an aluminum geometry or sintered inserts with geometries suited to many materials.
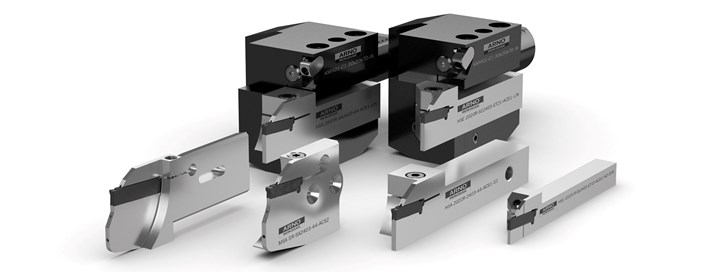
With its SA and SE range, Arno Werkzeuge offers a range of parting-off and grooving options for many applications and workpiece materials.
Arno Werkzeuge has also developed a third tool engineered for parting off small components with small diameters: The three-edged ATS system which can create a wide range of short, precise grooves. Here, the company says there’s value in its proven substrates and coatings. Plus, a countersunk clamping screw clamps the tool rigidly and precisely to the ground contact surface. ATS offers a large cutting depth of 6.5 mm compared to its compact dimensions (making it well-suited for Swiss-type machines). Groove widths start at a very narrow 0.8 mm and extend to 6 mm. For profile grooving inserts, contours up to 20-mm long can be mirrored on one insert. Variants with peripheral ground, sharp flutes are designed for operations with low cutting pressure on thin-walled parts. The ATS system can be used as a standard application for finish grooving O-rings or retaining rings in a single operation as well.
Quick Tool Changes
Shops that are seeing batch sizes decrease can find value in the company’s AWL/AFC quick-change tooling system. Two-part carrier tools make for fast tool changes that even less-experienced personnel can safely and easily perform.
With this, only the front part of the carrier tool is removed while the rear part remains on the AWL sliding head to act as a stop. This is said to ensure that the zero point remains constant. The two holder parts are joined by a connector system with an O-ring to secure the front holder part and prevent it from accidentally falling into the chip tray. In addition, a floating mount compensates for angular offset to ensure a high level of precision when changing tools, the company says.
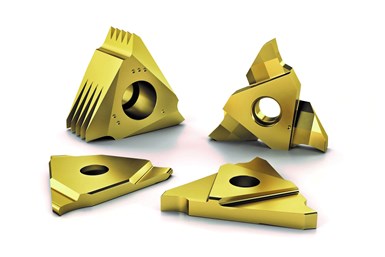
A countersunk clamping screw design is said to hold inserts rigidly and precisely to the ground toolholder contact surface.
Another example of Arno Werkzeuge’s user-oriented mindset is the ACS (Arno Cooling System), which was specially developed for parting off. The ACS 2 version features an internal coolant channel at the insert seat paired with a second coolant channel directed toward the bottom of the tool flank. The coolant channel is a 3D printed variant and has an optimized-flow, triangular end which supplies coolant across the full width of the insert right through to the edge. The company says some users report a 3 times tool life improvement.
The 3D printing process also can produce channels without right angles. This method also permits the production of a flow-optimized, triangular-shaped outlet that shapes the coolant jet to obtain maximum cooling effect with minimum consumption. In addition, the tool width can be reduced by 1 mm, which can provide workpiece material cost savings for high-production manufacturers.
RELATED CONTENT
-
5 Facts About Thread Rolling
Unlike subtractive processes, thread rolling does not remove material but instead moves and molds ductile metals quickly and precisely into the thread form using a cold-forming process. Learn more about thread rolling and tooling advances here.
-
Smart Workholding Device Measures and Monitors
Sensor and IIoT technology combine to enable these chucks and mandrels to automatically monitor workholding parameters and measure part features to ensure process stability.
-
Ceramic Inserts Can Boost Turning Productivity
When applied correctly, ceramic inserts can dramatically increase cutting speeds, providing shorter cycle times and cost savings compared to carbide for turning operations.