
This shop has adopted this flexible, machine-tending robot system that grips vises with parts clamped in them, not the actual parts. That way, only one gripper is required and reprogramming is not needed for new jobs. Photo Credits: Lang Technik
When Simon Oreskovic established his Zelos Zerspanung machine shop in 2017, he knew automation would be key to success. The managing director’s goal was to leverage quick-change workholding and robotic machine tending to establish an effective process for high-mix/low-volume work. For this to happen, he had to identify the type of automation technology that would enable his startup shop, located in Bessenbach, Germany, to machine a wide range of parts.
Oreskovic believes some robotic machine-tending solutions can be intimidating to small job shops. This can cause them to delay their transition to automated manufacturing because they think they need to invest in complex, expensive, process-specific systems that rely on highly trained specialists. “That’s not true,” he says. “You need to automate your job shop to remain competitive, but you can start small and adjust your level of automation to your future needs.”
Featured Content
This is especially important in high-wage countries such as Germany. In starting small with automation, Oreskovic first implemented quick-change workholding technology to speed setups. After that, he added a robotic loader and pallet-pool system to one of his three-axis machining centers. This enabled new jobs to be set up offline and installed in the pallet pool while the machine continued cutting another part, maximizing spindle uptime. Next, he integrated robotic systems for two machines in which the robot grips not the parts themselves but standard-sized vises holding parts positioned atop a trolley parked near each machine. That way, only one gripper is required to load various types of parts. This type of automation enables the shop to focus on parts no bigger than the size of a fist (which represents 80% of its business), while providing the flexibility to efficiently process batch sizes ranging from 10 to 1,000 pieces.
First: Quick-Change Workholding
Prior to opening his shop, Oreskovic gained machining and manufacturing experience working at his father’s manufacturing company, Automated Sewing Systems AG, also located in Bessenbach. His Zelos shop machines parts for his father’s company, but also for general engineering, machine tool, stage building and railway industries.
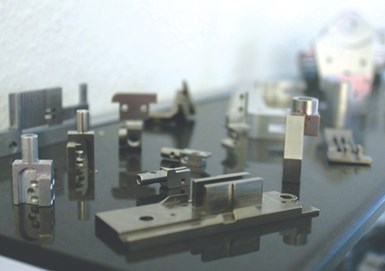
Nearly 80% of the parts Zelos machines are the size of a fist or smaller. This influences its decision on what type of robotic automation it integrates into its shop.
While working at Automated Sewing Systems, Oreskovic became familiar with quick-change workholding devices from Lang Technik, located in Holzmaden, Germany. (The company’s U.S. division is Lang Technovation, located in Hartland, Wisconsin.) This led him to purchase Lang Zero-point clamping systems and Makro-Grip 5-Axis vises for his shop to speed setups and provide high process reliability and repeatability, he says.
The Zero-point system uses an interface plate that mounts to a machine table to enable quick attachment of devices such as Makro-Grip vises to a repeatable position. Clamping studs installed on the bottom of devices such as the vises install into the plate’s receivers.
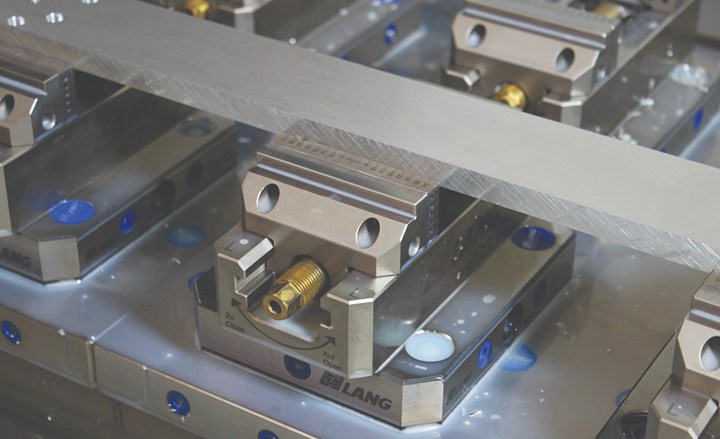
“Teeth” in vise jaws mate with indentations along the bottom of the part produced using a 20-ton stamping machine. This is how the device can provide high clamping force even though it grips just a small area of the part.
The Makro-Grip vises grip part blanks in an unconventional way. A 20-ton stamping machine is used to squeeze either side of a blank along its bottom and uses “teeth” that create multiple indentations in the blank. The blank then installs in the vise which has jaws with mating indentation profiles. This form-fit connection is said to provide high holding force even though the vise grips on only a small portion of the blank. It also provides ample access to five sides of the part during machining. After machining is complete, the indentations are milled away.
This is similar to workholding techniques in which a dovetail is machined into the bottom of a blank, and the blank is installed in a vise with a mating dovetail profile. However, a machine tool is required to create the dovetail profile, while the indentations for the Makro-Grip are created using the compact stamping machine.
Next: Robotic Loading, Pallet Pool
Lang provided support to help select the type of automated process that made sense given the size of Oreskovic’s shop and the parts it primarily would be machining. “Automation is typically associated with high-volume production runs, but it also pays off to automate low-volume, high-mix parts in job shops,” says Guiseppe Semeraro, Lang sales manager. “Once you have a more in-depth view of a shop’s needs, very often you can increase its productivity with simple, affordable and retrofittable automation solutions, including robots.”
The Lang Eco-Compact 20-workpiece palletizing and handling system was the first robot-loading automation system installed at Zelos. This system, which was added to the shop’s DMG MORI Milltap 700 three-axis machining center, features 20 pallet stations each with the capacity to hold 40 kilograms. The pallet pool enables the shop to set up and queue jobs while the machine is running. Each pallet features Zero-point clamping for repeatable positioning.
Finally: Robotic Loading of Vise-Clamped Parts
The Lang Robotrex was the second robotic machine-loading system installed at Zelos. In fact, the shop purchased two — one for its three-axis DMG MORI Ecomill 1100 machine and one for its five-axis Ecomill 50.
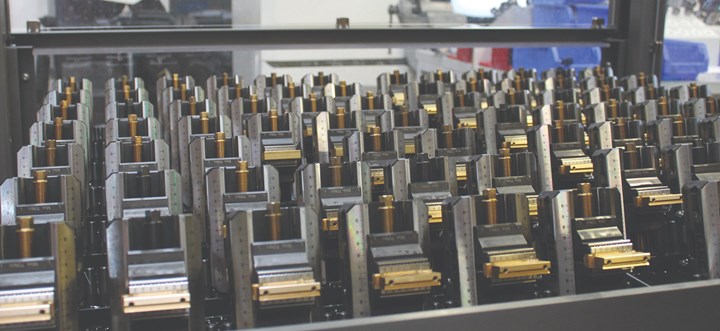
Depending on the part size, the automation trolley can store up to 42 vises. Optionally, Lang’s Robotrex system is available with up to four trolleys, which means that the storage capacity can be increased to up to 168 vices.
The Robotrex installs within an enclosure at the front of a machine and features a 12-kg-capacity FANUC robot. Each part blank is clamped in its own Makro-Grip vise, and those vises install in rows atop a trolley that is delivered to the Robotrex (the system can accommodate as many as four trolleys). Vertical orientation of the vises enables multiple vises to be installed on the compact trolley. Each trolley has a capacity to hold 30 vises with a maximum part size of 120 by 120 by 100 mm or 42 vises with a maximum part size of 120 by 100 by 70 mm. (These sizes fall in the range of the type of parts Oreskovic wanted his shop to primarily focus on.) The vises install in the machines’ Zero-point clamping system.
“This system takes away the fear as far as robots and grippers are concerned.”
Because the robot picks a common vise from the trolley and not parts of different sizes or shapes, only one gripper type is required and there is no teach-in process needed to accommodate new grippers for new jobs. “The beauty of this system is that it takes the fear away as far as robots and grippers are concerned,” Oreskovic explains. “Systems in which the robot grips the part to feed the machine might be efficient solutions for series production, but shops like ours need to have the simplest automation solution without the fear of robot reprogramming when parts change.”
Oreskovic says the most appealing feature of the Robotrex system is that it is compatible with almost any machine tool, and can be retrofitted to machines that do not have air or hydraulic supply, which is typically required for conventional automation systems. “The robot communicates with the machine tool via one M-code, which triggers the loading/unloading cycle,” Oreskovic explains. Loading is done through the machine door or a side window added to the machine. When needed, Lang adds the side window during Robotrex installation. Lang also connects the robot to the machine and programs the robot per the vises used at that time.
Oreskovic also appreciates the relatively low price point as well as compact design that require only 1.70 by 2.20 m of floor space. Plus, automation frees machine operators to work on the next order, set up new jobs on vises and to prepare new workpiece blanks using the stamping machine. He admits that he had concerns about running machines unattended overnight. However, the DMG MORI Messenger machine-monitoring system sends alerts when problems arise, and on-machine probes are used to measure cutting tools during the process. Oreskovic says this increases machining accuracy and reduces scrap and rework. Moreover, he and his team can monitor a machine’s status anytime via their smartphones. That said, for parts with very tight tolerances, the shop might split the job into two shifts, whereby roughing is performed unattended at night and finishing is performed during the day with an operator monitoring the process.
Oreskovic says the shop’s investment in automation has paid off, enabling it to achieve as much as 20 hours of spindle uptime per day. “We can also flexibly plan incoming short-notice orders, run the machines lights-out and also run them unattended over the weekend, so we have some spare time for our families, even being a small team.”
RELATED CONTENT
-
Smart Workholding Device Measures and Monitors
Sensor and IIoT technology combine to enable these chucks and mandrels to automatically monitor workholding parameters and measure part features to ensure process stability.
-
Bar Feeder Basics
Some primary factors are often overlooked when considering how to justify the implementation of a bar feeder for turning operations.
-
Checklist for Lights-Out Manufacturing
Many shops of various sizes are trying to hop on the lights-out bandwagon. This article looks at some things to consider and check out before “hopping.”