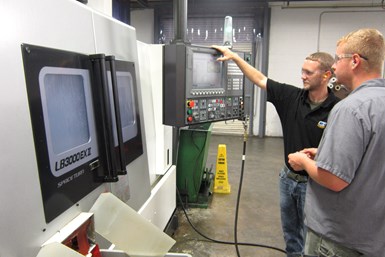
Around 3 p.m. each weekday, Custom Tool shop personnel begin setting up turning centers to run jobs lights-out during the evening.
For the Young brothers, shopfloor automation began by adding a bar feeder to an existing CNC turning center.
This happened very soon after Gillen and Bob Young purchased Cookeville, Tennessee’s, Custom Tool in 2008. (Gillen is president; Bob is vice president.) The bar feeder, which enabled a two-axis CNC turning center to run unattended for long stretches of time during staffed days, represented a significant shift in shop culture compared to how the company was previously managed. That is, automating a manual task was never contemplated to the extent that even payroll checks were still written by hand prior to the business acquisition.
Featured Content
Today, various automation examples have been implemented, and the shop benefits from them in various ways. For example, two new bar-fed, Y-axis turning centers with subspindles, live tooling and parts collectors can be set up to run overnight with the goal of machining parts complete while getting as much production time out the available 15.5 hours the shop is not staffed. Shopfloor employees, many now freed from simply loading and unloading machines, are better able to consider and suggest ways that processes can be improved. Oftentimes, these helpful suggestions have related to automating existing manual tasks (such as integrating part deburring into the machining cycle). In addition, new inspection technology has automated some measurement routines for multiple parts that were machined overnight.
Custom Tool has also recently automated data collection for its “production log” planning strategy it established approximately 10 years ago. The production log, which has become the backbone of its operation, reveals how effective the shop’s machines were during a day relative to expected daily production volumes, and shows how much “stolen time” the shop is pocketing. (This is the brothers’ nickname for the unstaffed 15.5 hours each evening.) It also helps identify jobs that make sense for overnight production as the shop looks to increase the percentage of annual lights-out-machining hours to 50% or more of its total production. As Bob says, that amount of unattended machining time equates to a second staffed shift at a much lower cost.
After the Bar Feeder
Bob Young manages the site operations, while Gillen (who also works as the chief architect IoT solutions for AT&T Consulting) is located in Atlanta, Georgia (although he visits the shop as frequently as time allows). The two decided to purchase Custom Tool after Bob, who previously worked for a machine tool distributor, was approached by the former owners who were nearing retirement and looking for an exit.
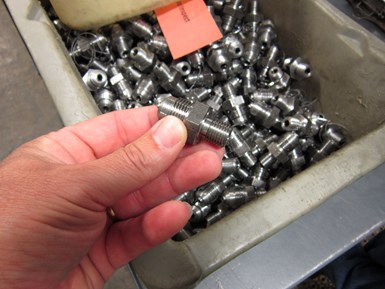
This fuel fitting is the first job the shop ran unattended overnight. It used redundant tools for the two threading operations to compensate for tool wear and doubled the number of parts that could be machined lights-out. Also, since this photo was taken, the shop has started using a special tool to perform in-cycle deburring to eliminate a secondary, manual deburring operation.
It became immediately clear to the brothers that changes to the company’s culture were essential. The two began working on instilling a mindset of continuous improvement with an eye toward implementing automation as much as possible. Given some natural attrition, they hired some new people, many relatively young and inexperienced, who were more open to embracing advanced technology and more apt to suggest ways to streamline processes.
After seeing the unattended-machining benefits of that first bar-fed turning center and envisioning a time when lights-out machining would become a reality, Custom Tool made a more substantial investment in 2012, adding a Y-axis Okuma LB3000 EX Spaceturn with live tooling, a subspindle and an Edge Technologies bar feeder to enable complete machining for some parts. The shop added another such machine in 2016 and a third in January 2019.
That said, it took time to reap the benefits of lights-out machining. The shop had to become comfortable with the new equipment and work to validate potential overnight machining operations. It then began running jobs for increasingly longer stretches of time into the evening until the shop was fully confident that they could successfully run through the night. Several elements were considered in the establishment of reliable unattended processes, and the shop has learned a number of lessons along the way. Some of these relate to:
- Coolant system. Unexpected drops in coolant pressure or interrupted coolant delivery can cause tools to break. Machines that run overnight require more maintenance than those that run only one shift. So, if a booster-pump filter is typically checked every few days for a machine that runs one shift, that filter must now be checked every day. In addition, Custom Tool’s second Y-axis turning center features a controller that sends a signal to stop the machine if it detects an issue with the coolant system.
-
It is important to consider chip management when developing a lights-out machining process as Bob Young explains to Senior Editor Lori Beckman. This unit features conveyor teeth that enable it to better handle long, stringy aluminum chips when the turning center runs unattended overnight.
- Parts collection. Initially, the chip hopper also served as the parts collector. Now, each turning center has an integrated parts collector. The size of the collectors must be able to accommodate overnight production volume. If the capacity is too small, then the number of large parts that can be produced overnight is limited. In addition, coolant comes out with each part that is collected, so some means of draining the coolant out of the parts collector and back to the machine’s sump is needed.
- Bar feeder. If parts for a job are sizeable, a bar feeder’s capacity might limit how many parts can be machined overnight. On the other hand, if cycle times are very fast, it is possible to consume all the loaded barstock, meaning someone would have to come to the shop to replenish the material so that overnight part production is not reduced.
- Redundant tooling. A fuel fitting part with two types of threads shown was the first job that Custom Tool set up to run overnight using redundant tools. When this job ran with an operator standing by, that operator could tell when an offset change might be needed due to tool wear. However, the shop found that it initially could only run that job lights-out for four hours, because it was at that point in which offset adjustments were needed for the two threading tools. Recognizing that, the shop started using redundant threading tools, calling for a tool change at a certain part count just prior to when tool wear became an issue. Although the shop does not get all the potential life out of its threading tool inserts, the additional time the machine can run unattended justifies this.
- Load monitoring. With spindle-load-monitoring capability, when the load goes to zero, that means a tool has broken. Part programs are written so that the machine stops at that point rather than continuing to run the job and risking breaking subsequent tools.
- Measurement capacity. It is nice when hundreds of parts can be machined overnight, but that unattended production has changed what some Custom Tool shopfloor employees do to start each day. Time must be set aside for part segregation, inspection, machine evaluation and setup for the next job. In fact, part inspection became a bottleneck when the shop first implemented lights-out production. To speed inspection routines, Custom Tool added a Keyence IM series image dimension measurement system, which can automatically measure and record numerous external part features on one or more parts set up on the device.
Automating Production Logging
The production log Bob implemented in 2011 reveals how productive the shop’s nine CNC machines and one robotic welding cell are each day by comparing daily planned work for each with actual production achieved. It also reveals how effectively the shop is making use of the available overnight hours.
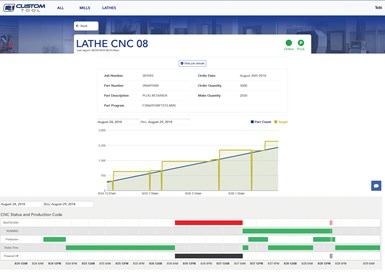
The automated data gathering system collects production information from machines every 20 minutes. It also pulls job data from the shop’s ERP software. Reports can then be created to more graphically show production log information. Photo credit: Custom Tool
Until recently, all this data has been collected manually. Each hour, employees log part-production numbers hourly for each machine and enter those values as well as machine-status codes into the production log spreadsheet. The shop strives to maximize the values of codes 10 and 15, representing production time during the shop’s single day shift and unattended production time overnight, respectively. Comparing these values with expected daily production reveals true machine utilization, Bob says. Other codes, such as those for setup, rework and time waiting for material, tooling or operator attention, shed light on precisely how long it takes to complete a job in addition to the actual machining time.
Common variables have been set up to track the status of each job. Part count is handled by G code and increases by one each time a part cycle is completed. Other variables require operator input. These include run target (the machine will pause when the part count reaches that value), job number (this is listed on the job traveler) and production log code (this shows when production status has changed).
The production log helps identify processes that lend themselves to lights-out operation. If a machine set up to run all night is not getting close to the 15.5 available hours, then it might be that this job is not well suited for running overnight. Or, if one machine runs all night and another runs half the night, perhaps it makes sense to push the job that ran only half the night to a different machine and replace it with work from the other, longer running machine to achieve higher utilization. The production log also serves as a diary of sorts, because it is used to document issues such as tool breakage or bar-feeder malfunctions that caused machines to fall short of targeted production values.
The shop continues to work toward the scenario in which no one will need to visit machines each hour to collect and enter data for the production log. This is thanks to an automated data collection and reporting system Gillen is developing that uses a web-based, Industrial Internet of Things (IIoT) platform to pull data from machines that have agents for the open-source MTConnect communication protocol as well as the company’s Jobboss enterprise resource planning (ERP) software. The platform is Devicewise for Factory from Telit, a company that offers IIoT modules, software and connectivity services and software.
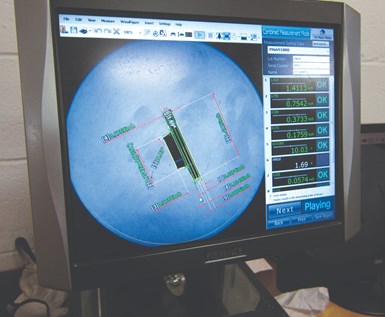
Lights-out machining means a lot of parts are waiting for shop personnel when they arrive in the morning. For Custom Tool, this created an inspection bottleneck that spurred the shop to add an image dimension measurement device to speed part measurement for quality control personnel.
Gillen says the benefits of this system are that it interfaces with a variety of controllers and no custom programming is needed for data collection. It is configured to automatically pull all data that was previously collected manually from the machine (part count, machine code and more) as well as ERP data (job number, job description, order date, order quantity, delivery date and more) and stores it in the cloud. Data is accessible via a web dashboard. Reports can then be created to more graphically show what was previously available in the production log spreadsheet.
The system has been collecting data every 20 minutes since early June 2018 without missing an entry for a machine that was running. Gillen says there are many good machine monitoring products available. However, his technical background afforded an opportunity to explore an in-house solution that addresses the business information the shop is most interested in knowing. He also feels this data collection capability might also lead to even more advanced analytics, such as tying cut time to specific types of cutting tools or inserts.
RELATED CONTENT
-
A Beginner’s Guide to Automation
While many shops are enjoying the production benefits of robotic part handling, others are struggling to tackle the first steps of implementation. Here’s a basic guide to help provide clarity on where to begin.
-
The Effects of Automation on Manufacturing
Companies that are not currently using automation in their manufacturing processes should be considering it.
-
Introduction to Industrial Artificial Intelligence
The systematic implementation of Industrial Artificial Intelligence enables secure data sharing among manufacturers, remote monitoring and operations, managing geographically distributed assets and more.