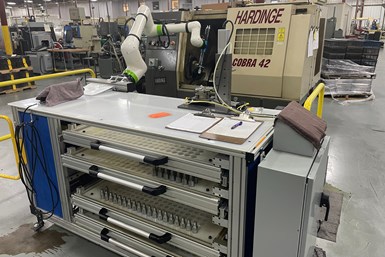
RW Screw believes adding robots to legacy equipment that remains accurate makes sense. Here, a cobot tends to a Hardinge turning center. This robot station with drawers for stock and completed parts is bolted to the floor to prevent any “walking” due to robot motion, given the precision positioning required to install workpieces into the chuck’s collet.
Massillon, Ohio’s RW Screw currently employs approximately 230 people. Bill Reeder, president of the 74-year-old contract machine shop, says an optimal staffing level given its equipment capacity is approximately 265. The company has more than 200 machine tools, including VMCs, Swiss-types, single-spindles, multi-spindles, rotary transfer machines and grinding machines as well as secondary machining and finishing equipment. Unfortunately, a small number of these might sit idle at times because there’s nobody available to operate them.
One reason is there are many manufacturing businesses in the northern Ohio area all competing for the same people. On top of that, Amazon recently opened a new fulfillment center in nearby Canton that is expected to create 1,000 new jobs. The personnel challenge has gotten to the point where RW Screw has realized that implementing automation and technology that can reduce human involvement in manufacturing processes are necessary to maintain success moving forward.
Featured Content
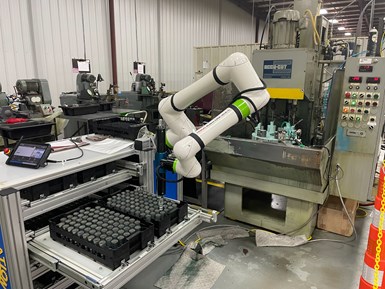
Here is another example of a new cobot effectively tending an older — albeit precise — honing machine.
In fact, Reeder says the company evaluates opportunities to automate processes not simply with an eye toward becoming more efficient per se but rather as a requisite means to an end to ensure it continues to deliver products on time and to specification to its customers as expected.
Adding robots to tend manufacturing equipment is one part of its solution. The company recently installed six robots in a span of seven months and plans to add 10 more this year. That said, Reeder notes that none have or will eliminate anyone’s job there. Instead, employees can be redeployed to perform duties that can more valuable than loading and unloading machine tools, for example.
Over the years, RW Screw has also learned lessons about integrating automation as a means to reduce or eliminate manual operations as Reeder explained to me during a recent visit. One of these is that automation is more than robots, citing how the company has considered how inspection, tool measurement and workholding devices as well as the type of barfeeders it uses can streamline work on the shop floor.
But, during my visit, Reeder also pointed to three tactics that RW Screw applies with regard to automation integration that I feel is worthy of consideration both for shops that are new to automation and those that are experienced with it. Those tactics include taking time while integrating robots, creating an automation steering committee, and working to develop automation engineers, not necessarily manufacturing engineers.
Robot and Other Automation Additions
E. Ray Woolley founded R.W. Screw Products Inc. in 1948. Now known as RW Screw, the company has a facility with more than 200,000 square feet of manufacturing and administrative space.
The shop’s first significant step into robotic automation was integrating a Denso robot itself to load and unload shafts into a spline-shaping machine. Conveyors are used to both deliver new workpieces to the robot and collect completed parts after machining.
RW Screw has also installed a number of collaborative models (aka cobots). For instance, a number of FANUC CRX-10iA/L six-axis cobots tend equipment such as turning centers, honing machines and grinding machines, some of which are legacy equipment, but remain highly accurate.
Reeder says the company appreciates the cobots’ robustness, which offer a 10-kg payload and 1,418-mm reach as well as FANUC’s customer support. And while these cobots are designed to be redeployed from one machine to another, the shop has each dedicated to one specific machine. Most are attached to tables/stands with drawers used to present raw material to the robot and collect completed parts once machined. The shop bolts these stands to the floor to prevent any possible “walking” due to robot motion.
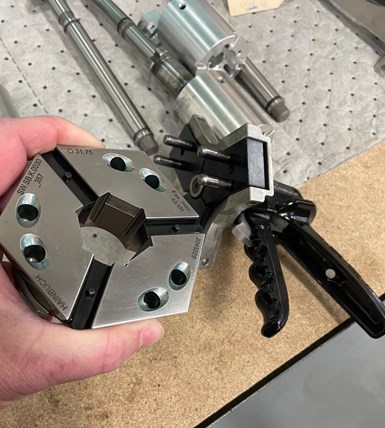
Changeovers for rotary transfer machines, multi-spindles and other turning centers are now faster using quick-change collets.
But, the shop considers other equipment that can either automate a process or reduce the time and amount of human intervention. Quick-change workholding from Hainbuch is an example of the latter. In fact, it was a write-up that Hainbuch produced, portions of which I paraphrase in the following paragraphs, that spurred me to visit RW Screw to learn more about the shop’s improvement efforts in the first place.
The shop uses Hainbuch Hydrok hydraulic stationary chucks in its Hydromat and Schutte rotary transfer machines. Jason Schoemann, sales engineer at Hainbuch America, points to RW Screw’s 12-station Hydromat Eclipse machine fitted with Hydrok SE 65 hexagonal chucks with a clamping range of 3 to 65 mm. “The Hydrok SE 65 is well suited to the size range of the RW Screw’s parts family, and the hexagonal geometry offers optimal protection from contamination, increases tool life and delivers 25% greater clamping force,” Schoemann says. “It accommodates both round and hexagonal bar stock with clamping heads that can be quickly and easily changed.”
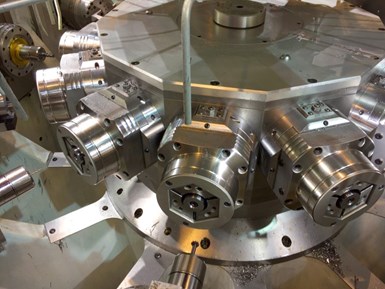
RW Screw’s 12-station Hydromat Eclipse rotary transfer machine is fitted with Hainbuch Hydrok SE 65 hexagonal chucks that are said to provide 25% greater clamping force than conventional devices. Photo Credit: RW Screw
For collet changeovers, an operator uses a pistol-grip-style device with pins that he or she inserts into the face of a collet and squeezes the handle. A locking mechanism in the handle keeps the fixture collapsed while installing and removing the collet. Pressing a trigger unlocks the changing fixture and releases the collet.
“The Hainbuch quick-change feature is essential to achieving our production goals,” Reeder explains. “What used to take one or two days to change between parts now takes 30 minutes, and we can go from a hex stock to round stock in 3 hours. Equally important to successfully holding tolerances is the high repeatability of the Hainbuch system due to precision grinding. Also, the extra 25% rigidity reduces chatter, which is a critical factor when turning hex barstock.”
Examples of other equipment the shop has found to automate processes beyond adding robots include:
- Magazine bar feeders. Bar feeders are commonly used in most high-production machine shops, but they come in various designs. RW Screw finds value in magazine models that enable large bundles of barstock to be loaded to achieve long stretches — perhaps three shifts — of unattended machining. It has added these to rotary transfer and multi-spindle machines in the form of Cucchi BLT and Edge Technologies’ FMB brands that accept 12-foot bars to further extend unattended machining time and reduce machine downtime.
Magazine bar feeders that accept 12-foot bars extend unattended machining time and reduce machine downtime at RW Screw for equipment such as rotary transfer machines.
- Tool presetter. A tool presetter automatically measures offsets so an operator doesn’t have to do that at a machine while installing new tooling for a new job. RW Screw uses an Origin tool presetter from Omega TMM, which the device manufacturer says fits the industry need for an entry level shopfloor optical tool presetting device. Tooling for new jobs are then kitted and delivered to a machine’s work cell to await installation.
Thanks to a tool presetter, tooling for new jobs can be easily measured then kitted and delivered to a machine’s work cell to await installation for a new job.
- Vision inspection devices. Noncontact measuring instruments using cameras to measure parts can greatly speed inspection processes. In one example, a time study revealed that a person who was tending to two machines spent 60% of his time gaging parts at the machine. Now, those measurements are taken automatically on a Keyence vision system to enable that person to tend three machines. The shop also created a cell for parts that require 100% inspection that uses a bowl feeder to supply parts to an enclosed vision system and touch probing station to automatically measure them while sorting the good from the bad.
At one point, a technician would spend 20 minutes each hour gaging these complex shaft parts. Now, this Keyence vision system automatically measures those parts nearly instantly to free the technician to perform other value-adding duties.
Automation Lessons, Advice
Three practices that RW Screw implements as part of its approach to applying automation stood out to me during my conversations with Reeder. Listed below, these ideas might be worth considering both if you’re in the early stages of automating processes or have been integrating automation for some time.
- Take time while integrating robots. Integrating its first robot taught RW Screw not to rush these projects, especially in a high-production environment. Today, the shop creates “mock” machines — jigs that mimic actual machines — to use while programming a robot, identifying touch points, dialing in the process and so on. Tweaking the process with the robot in front of the actual machine not only can this extend machine downtime, but it might cause employees to second guess the value of robotics if they’re dealing with issues for a period of time after integration.
- Establish an automation steering committee. RW Screw created an automation steering committee that meets weekly to discuss proposed automation projects. Once a quarter, the committee looks closely to identify projects with which it makes sense to move forward. As part of these efforts, Reeder and other managers take regular walks on the shop floor to engage employees and learn about any production pain points. The solution to an issue might be to add a robot, but it also could be to add some other technology to open a production bottleneck that exists because of a manual operation.
- Develop automation engineers. In the past, RW Screw focused on developing manufacturing technicians, experts on how to machine a part, how a tool or collet works and so on. That’s still valuable. However, it has pivoted a bit to develop automation technicians who understand robots, automated gaging and various other forms of shopfloor automation. As Reeder notes, the shop can’t afford to have its maintenance personnel continuously making robot touch point changes their entire shift. All personnel must learn how to perform duties such as that, and the shop will continue to invest in that type of training moving forward.
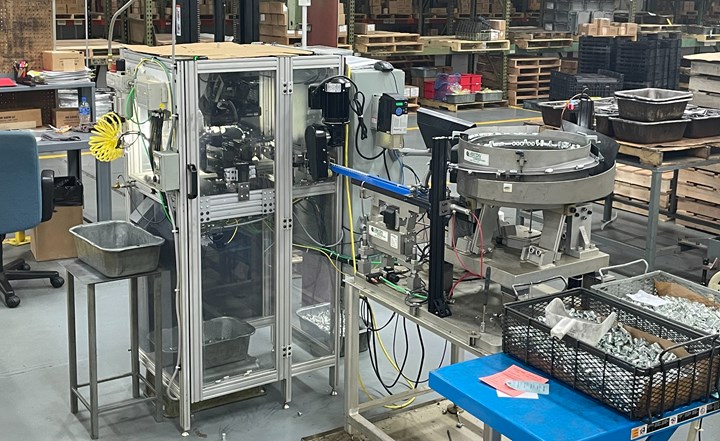
Previously, this high-volume job required nine people over three shifts to perform 100% part inspection. Therefore, RW Screw engineered this process that uses a bowl feeder to supply parts to an inspection cell that includes a vision system and touch probing to automatically measure all parts and sort the good from the bad.
RELATED CONTENT
-
The Value of RFID Machine Operator Authentication
Can secure shopfloor employee authentication via radio frequency identification enable shops to optimize their data-driven manufacturing efforts?
-
Consider This Another CMMC Reminder
Machine shops serving the military/defense industry that currently aren’t working toward achieving Cybersecurity Maturity Model Certification could be caught flat-footed once it’s required.
-
Production Machining's February 2024 News Highlights
Production Machining’s February 2024 news highlights include new facilities and expansions, partnerships, anniversaries and more.