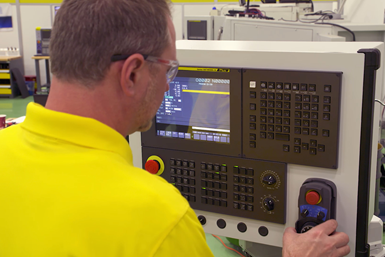
Those who are familiar with G-code programming can use the Quick and Simple Startup of Robotization feature in FANUC CNCs to more easily program FANUC robots. Photo Credit: FANUC America
Although the potential benefits of machine-tending robots are clear to many shops, those with no robot experience might be apprehensive about programming them and connecting them to a machine tool. However, robot manufacturers continue to develop technology to streamline and simplify this, and the new Quick and Simple Startup of Robotization (QSSR) G-code feature from FANUC America is one example.
According to the company, QSSR G-code can reduce the time to connect and program a robot by 55% — from 15 hours to approximately 6 hours.
Featured Content
The QSSR G-code feature enables machine shop personnel to program FANUC robots through a FANUC CNC using the ISO-standard G-code format. It is designed for those who are familiar with G-code programming, but not robot programming languages, making additional training for robot programming unnecessary.
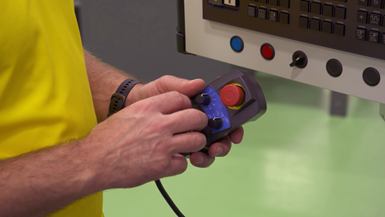
During programming, robot motion is controlled via the CNC’s MPG and stored for automatic program creation. Photo Credit: FANUC America
A single Ethernet cable is used to enable communication via FANUC’s FL-net Fieldbus protocol between the robot control and machine CNC. The QSSR G-code feature is available on FANUC CNC Series 0i-F, 0i-F Plus, 30i-B and 30i-B Plus controls used on many of the company’s machining centers, turning centers and EDM equipment. On the robot side, QSSR G code is available on the iD Plus model controllers. (In some cases, a software upgrade to different CNC or robot controller software can support QSSR G code functionality.)
Those familiar with CNC G-code programming can program a robot.
Robot programming is accomplished utilizing menu-driven teach functions. QSSR G-code does require some knowledge of Programmable Machine Control ladder-logic programming within a FANUC CNC. However, function blocks with pre-written PMC ladder logic code can be used.
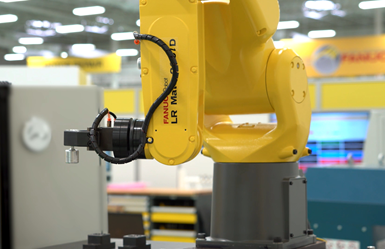
The QSSR G-code function is available on a number of the company’s CNC models and robots featuring the iD Plus controller. Photo Credit: FANUC America
For robot programming, an operator selects the desired robot coordinate system from the CNC and the robot can be moved to specific locations using the CNC’s manual pulse generator (MPG). This reduces the reliance on a separate teach pendant for the robot. The movement of the robot is learned and a robot G-code program automatically created. This program is then stored on a dedicated program path for the robot.
The company says QSSR G-code was designed to help shops get started down the path of robot integration and programming for machine tending. But, once shops gain experience adding automation in this way, they will become more proficient and likely will be less reliant on the function.
RELATED CONTENT
-
Adding 5-Axis Capability to a 3-Axis CNC Mill
This attachment provides shops using thee-axis machining centers the option of on-demand four- and five-axis machining.
-
A Fitting Machining Process
Diversified Fittings has turned to twin-turret/twin-spindle equipment and machine monitoring to become more efficient producing hydraulic fittings and adaptors.
-
Let’s Talk About Less Machining Chatter
For some turning work, unwanted harmonics can cause chatter and poor surface finishes. A new CNC software capability can automatically compensate for this.