Learn How Workholding Helps Whip Rotors Into Shape
Hainbuch America’s custom workholding will be on display at IMTS 2022.
#imts
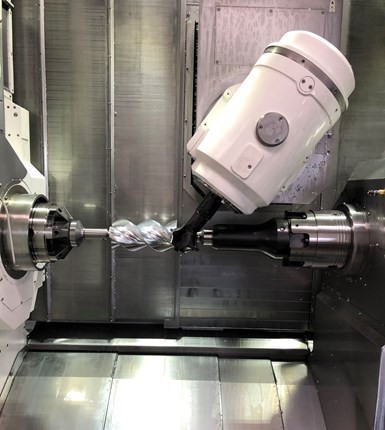
Whipple Superchargers machines the profile for each rotor to ±63 microns with the goal of achieving a clearance of approximately 125 microns between each pair in a supercharger. Rigid workholding from Hainbuch is critical to help repeatably achieve these accuracies while providing clearance for B-axis machining. Photo Credit: Hainburch America
Those of you into automotive or marine racing might know about Whipple Superchargers’ twin-screw superchargers. The key for optimal performance with these types of power-adders is the accurate, non-contact meshing of two helical rotors inside a supercharger casing. That means the rotor machining process must be on point to deliver the requisite precision to ensure Whipple Superchargers’ units deliver higher efficiencies to competitor designs.
Custom workholding from Hainbuch America Corp. is a big part of this, helping increase part-holding rigidity during machining on a B-axis turn-mill while providing sufficient clearance for the tilting B-axis head. In addition, changeovers are now two minutes compared to 10 minutes when Whipple Superchargers used extended-length, pullback-style ER collets to clamp on rotor shaft journals. Now, by using dead-length collets that “clamp in space,” the rotor blanks will not move when the collets are clamped. As a result, no additional load that would have to be dialed-out is applied to the machine’s main spindle.
How do I know all this? I once visited Whipple Supercharges to see this in action. Now, you can learn more about it at a display in one corner of the company’s booth 431636 in the West Building. This display showcases two rotors used in a Whipple Supercharger slowly rotating so visitors can see the precise fit between them. And while asking more about this application, don’t resist pushing the display button to hear the sound of the supercharger in action.
Also, be sure to also check out another display Hainbuch created that emulates the look of a CNC turning center to enable the company to demonstrate its centroteX S chuck changeover system in an unobstructed manner. This is a good example of the type of workholding technology is important especially given the trend toward high-mix/low-volume machining work.
RELATED CONTENT
-
Starrett's Multisensor Vision System Provides Large Field of View
IMTS 2022: The AVR-FOV 0.14X multisensor vision system is designed to provide accurate, efficient measurements fora wide range of parts.
-
Marubeni Citizen-Cincom Twin-Turret Lathes for Flexible Tooling
Miyano machines are designed to ensure high rigidity, high accuracy and long life.
-
Questions about Precision Machining? Ask Index
At this IMTS, Index Corp. is challenging show visitors to Ask Index key questions, the answers to which can help them ready their businesses for the next five years or more.