The most essential quality for any automotive vehicle (whether it be car, truck or bus) has nothing to do with speed, aerodynamics or aesthetics. Safety is and always will be the top priority.
Especially when it comes to race cars. The dangers drivers face are multi-faceted — the astonishing speed just one aspect to consider. Therefore, it’s imperative that precautions be implemented to promote driver safety.
Featured Content
To address the challenges associated with driver safety in professional racing, IndyCar is utilizing additive manufacturing (AM).
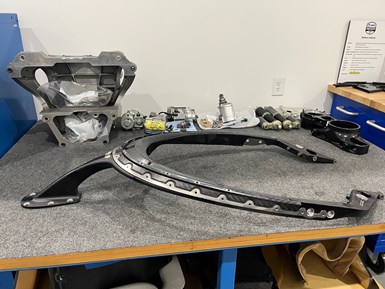
The image above depicts a finished top frame prior to being added to a race car. The safety device functions to promote driver safety in the event of impact or falling debris.
Most recently, this utilization has resulted in the creation of a safety device known as the top frame, a mechanism to protect drivers in the event of a rollover or from flying debris due to collision.
My colleague Stephanie Hendrixson and I recently had the chance to visit IndyCar’s headquarters in Indianapolis to learn more about the safety device being implemented in its race cars. We spoke with Tino Belli, IndyCar’s director of aerodynamic development, Mark Sibla, IndyCar’s chief of staff and Dominic Coffey, the design engineer and project manager of one of IndyCar’s partners, Dallara.
We also had the opportunity to tour the IndyCar Series’ most famous racecourse, the Indianapolis Motor Speedway, where we saw firsthand the unbelievable speed at which these cars average and why safety measures are so important to prioritize.
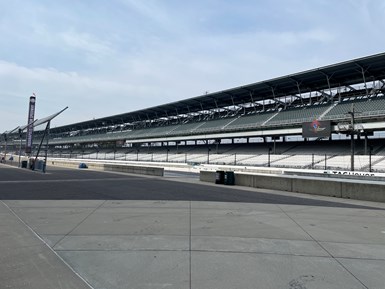
The speedway above is none other than the Indianapolis Motor Speedway, home to the NTT IndyCar Series’ most famous race, the Indianapolis 500. Drivers from around the world come compete at the annual Memorial Day Weekend event featuring a season-high 33 entries.
IndyCar 101
For those unfamiliar with IndyCar Series racing, here are the details to know when distinguishing it from other types of racing.
IndyCar serves as the sanctioning body for the NTT IndyCar Series (creating the regulations and orchestrating all of the racing).
Additionally, IndyCar completes all of the technical inspections for the race cars as well as monitoring the racing itself to further ensure driver safety.
Tino Belli says that the difference between the IndyCar Series and other types of racing lies in a combination of factors. “IndyCar focuses on competitive racing rather than the engineering design part. All the race cars we race are exactly the same, open-wheel models. Therefore, it’s more about the racing itself rather than the car being raced. This is a main distinction between the IndyCar Series and Formula 1,” Belli says.
Competitive racing demands a variety of tracks for increased challenge — the diverse schedule ranges from super speedways to street circuits to road courses and even to short ovals (another distinguishing factor from other types of racing). The track surfaces themselves can differ for IndyCar Series racing, as some feature bumpier layouts than others.
IndyCar Series drivers come from all over the world to compete, representing more than 15 different countries. Racing is the ultimate test of physical and mental strength of its participants.
At speeds up to 240 mph, both the stakes and dangers are high. Which is exactly why added precautions and safety measures are built in to the cars to ensure driver survivability in the event of a collision.
An Additive Course
The additively manufactured top frame is one such built-in feature. In addition to holding the car’s aeroscreen in place to protect the driver from debris, it can potentially save a driver’s life in the extreme case of a rollover.
This effective safety device was created with the help of the quick-turn pace that additive affords for product development and experimentation. With a tight deadline to meet, IndyCar was able to employ additive to generate its key safety feature on race cars in record time.
“The project time frame was very short, the gestation beginning in May of 2019 and the first model being tested at the Indy 500 track in October of the same year,” Belli says.
Originally, the idea was that the initial design would be created via titanium casting, but ultimately 3D printing was chosen as the manufacturing method instead. Additive enables a variety of unique shapes and wall thicknesses that are available much more readily than traditional forms of manufacturing, especially factoring in the tight time limit the IndyCar team was working with.
The debut of the completed IndyCar top frame came in 2020 and the quick turnaround was a direct result of a combined effort involving various levels of expertise from the additive industry.
Design Considerations
When creating the top frame’s design, there were various factors at play.
Coffey mentioned one such factor that seems so simple but is hugely important in racing: ergonomics. How quickly can a driver get in and out of their car with the addition of the top frame?
Another forefront consideration is aerodynamics. The top frame required a design that would be light enough to accommodate smooth movement and speed of the race car but also strong enough to protect the driver in the event of impact.
Lastly, ensuring the top frame would seamlessly attach to the monocoque was a factor in its overall design and application.
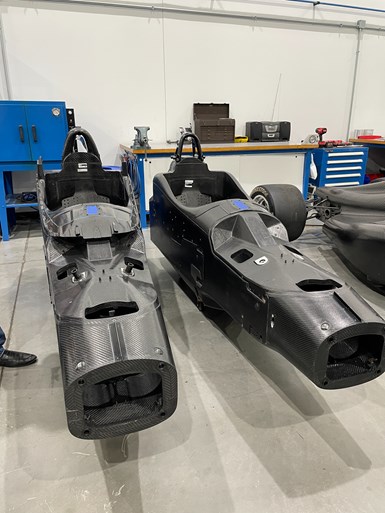
Two IndyCar monococques pictured side-by-side. The monocoque serves as the shell of the race car, supporting, protecting and holding together all additional features (like the top frame).
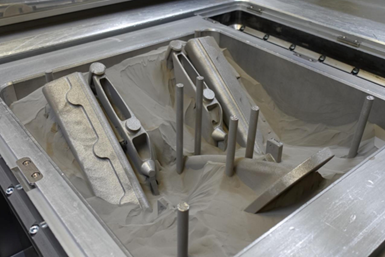
Pankl utilized laser powder bed fusion 3D printing via EOS machines to print the top frame in five separate, titanium parts. Photo Credit: Pankl Racing Systems AG
Manufacturing the Top Frame
The 3D printed titanium top frame was designed by Red Bull Advanced Technologies, along with the aeroscreen and composite structure on the monocoque to nest the top frame.
Once the design had the green light, Dallara, an Italian race car manufacturer with a location in Speedway, Indiana, and the main manufacturer of IndyCar’s race cars, stepped in. Dallara focused on most of the aerodynamic work, for example, factoring in the wind tunnel testing to ensure the top frame integrated smoothly into the car’s structure and wouldn’t hinder speed.
IndyCar also connected with Aerodine, a local composite company that created the composite lower frame (which bonds to the cockpit opening where the top frame and aeroscreen both attach).
The top frame was designed to print in a single build. Austrian company Pankl Racing Systems 3D printed the top frame pieces using the laser powder bed fusion process via EOS machines. Because the 3D printer is not large enough to print an entire top frame in one single piece, it prints the device in five separate pieces on one build plate.
Post-print, the separate pieces are welded together and post-machined to create the final product to enhance the race cars. The finished top frame is then delivered to Dallara in the U.S., where a composite Z frame is installed. The Z frame is bonded to the titanium frame to accommodate the carbon top pairing that coats the aeroscreen.
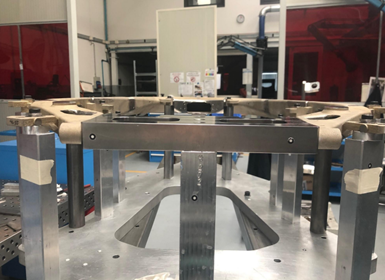
This image captures the welding process of the top frame after the pieces have been 3D printed. Photo Credit: Pankl Racing Systems AG
The original IndyCar top frame design had 14 main fasteners that hold it secure to the chassis.
Testing and Initial Implementation
According to Belli, the top frame underwent a series of load tests to ensure its strength and durability to survive a crash at high speed.
The device was loaded with 150 kilonewtons (equal to about six or seven Chevy Silverado trucks in weight) to two locations on the frame (one on the front of the device and the other slightly towards its side).
The top frame was tested to make certain it would be able to withstand and deflect falling debris at high speeds and winds associated with this.
After successful testing followed by trial runs, the original IndyCar top frame was off to the races.
First-Generation Success
The finished frame weighed in at less than 30 pounds, despite it being able to withstand a load in excess of 34,000 pounds of force in the event of impact.
The original top frame was produced in a series of 66 individual devices, as there are a total of 33 cars at the Indianapolis 500, the NTT IndyCar Series’ largest race. IndyCar required two top frames per car to ensure each car had a spare.
This model of the top frame has been used since its debut in 2020, having three seasons under its belt without the need to print more (speaking to its durability). So far, the only time a top frame has been damaged has been when a car was turned upside down and inverted on the track. And even then, the damage was minimal, as there was just some slight rubbing away of the surface of the titanium where it met the asphalt.
The top frame can be seen on the very top of this completed IndyCar Series race car and it is complete with the aeroscreen attached (the clear screen).
The advantage here? Had this crash occurred prior to the inclusion of top frames on the race cars, the carbon fiber of the monocoque cockpit opening would have all but rubbed away, not only creating an irreparable problem but endangering and leaving the driver vulnerable inside.
With the addition of the top frame, all of the monocoques that have experienced slight rubbing have still stayed intact, likely saving lives, money and ultimately time in the long run.
Next-Gen Top Frame On Track to Arrive in 2024
Looking to the near future, the next generation of top frames will be added to the IndyCar Series race cars come 2024.
“The optimization of 3D printing when the project began is very different than where it is now,” Coffey says.
As previously mentioned, the original project required a quick turnaround time, which made additive the right choice for design iteration and production. Since then and learning from the original design, Pankl has been able to topologically optimize material thickness via further 3D printing experimentation. Now, the company says generating consistent wall thicknesses throughout the frame isn’t even a necessity after optimization.
Equipped with this new depth and knowledge for optimization, the weight of the top frame has been significantly reduced. The weight reduction is beneficial in terms of the car’s center of gravity and ultimately, vehicle dynamics. Additionally, an added bit of material on the front fastening will serve to further fortify the strength of the frame. In total, seven pounds of unnecessary weight have been removed from the top frame in its new design.
“In racing terms, seven pounds is a massive amount of weight. The top frame is located high up on the car and therefore must be as light as possible to ensure the center of gravity of the vehicle remains as low as possible. The new, lightweight top frame should see significant improvement, especially as the center of gravity has a direct effect on a car’s tire wear,” Belli says.
Besides the top frame itself, another element undergoing optimization was the installation process itself. The original fastening of the upper frame to the chassis was one such detail that was improved upon, Coffey says. Two of the bolts for the fastening were originally obscured by the frame itself, thus requiring an open-end torque wrench for installation.
With the new top frame, it is much easier to install and uninstall those two bolts, assisting in assembly but also in the event the safety team needs to disassemble to extract a driver.
With this ease of installation, utilizing 3D printed parts for race cars “Is becoming more of a standard practice,” Coffey says. Another component that will be added to the cars for the 2024 racing season is a duct to feed cool air to the driver’s helmet. These air ducts will be 3D printed in polymer.
In lieu of additive optimization, it is safe to say the next-gen top frame is ready to go in terms of providing even more security for the drivers to come.
RELATED CONTENT
-
Video: Why a Production Machine Shop Started a Baseball Bat Company
A 153-year-old manufacturer of precision, metal pins recently started a side business creating custom wooden baseball bats. The reasoning behind establishing this new company is intriguing, as is how it has helped create a stronger bond with the local community.
-
Adding Additive Manufacturing to a CNC Machine Shop
With many types of metal and polymer 3D printing methods available, it might be difficult to identify the type that could be best implemented in your shop. Here is a rundown of these 3D printing processes along with how each can be used together effectively in a CNC machine shop.
-
In-Machine Probing Possibilities for VTLs
A manufacturer of vertical turning centers uses a “push/pull” optoelectronic probe with custom bracket to enable its machines to perform effective, in-process measurement of shafts and related automotive components.