Cutting Tool Considerations for Hydraulic Port Machining
Indexable insert cutting tools can boost the efficiency of port machining processes by creating multiple features in a single operation.
#techbrief
Edited by Derek Korn
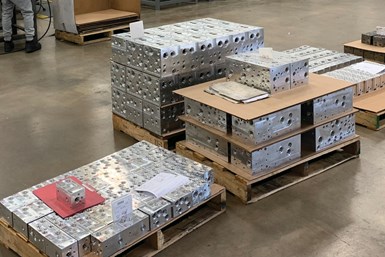
Machining ports in hydraulic manifolds can provide unique challenges. (Photo Credit: PM)
There are a few key aspects of effectively machining hydraulic ports that shops should keep in mind. One is knowing about the properties of the workpiece material. Elastic materials such as aluminum, low carbon steel and stainless steels are most often used for these applications. Here, it is about getting the finish that’s required, especially if there is a callout on a seal angle diameter or even the spot face, which may require a secondary operation to clean the finish.
When drilling in aluminum — a material that is commonly used for hydraulic manifold applications — solid carbide tooling can struggle because the big chips that might be created can become stuck in the manifold cavities, which might require a subsequent cleaning process so that tools used for additional operations are not recutting those chips. This can be circumvented by using an alternate tool with optimized geometry which creates smaller chips.
Featured Content
Also, consider the number of drills or type of drills being used. Traditionally, multiple solid carbide tools have been used for port cutting applications. For example, a spot drill that might be used to prep the port hole is followed by a standard tool to drill the minor diameter of the thread, while another tool is used to create the port contour afterward. Conversely, dedicated port form tools that are typically brazed on carbide would need to be taken out of the toolholder once the tool is used to the end of its life. While a fresh tool needs to be put in and then touched off to begin machining again, the worn tool that was taken out needs to be sent out to be resharpened and recoated, which can be time consuming and lead shops to carry more tooling inventory.
Indexable porting tools offer a solution. One example is Allied Machine and Engineering’s AccuPort 432, which performs multiple operations in a single step while enabling shops to swap out worn inserts and return to production. Indexable tools such as these provide high repeatability and surface finish while eliminating lost production time due to predrilling setups and regrinding, the company says. With four-in-one tools, not only do shops get the tap drill size required, seal angle diameter, form and spot face but they can also drill from solid.
For port cutting, these types of indexable tools offer a specific geometry to create a better chip in elastic materials which can realize a better surface finish. And, in addition to optimizing the inserts on the front of the tool for a given material, using point geometry can help reduce thrust and keep the tool centered as it is guided through the cut to achieve the tight tolerances that are often required. Port form inserts are also replaceable and often available in different substrates to best match the workpiece material.
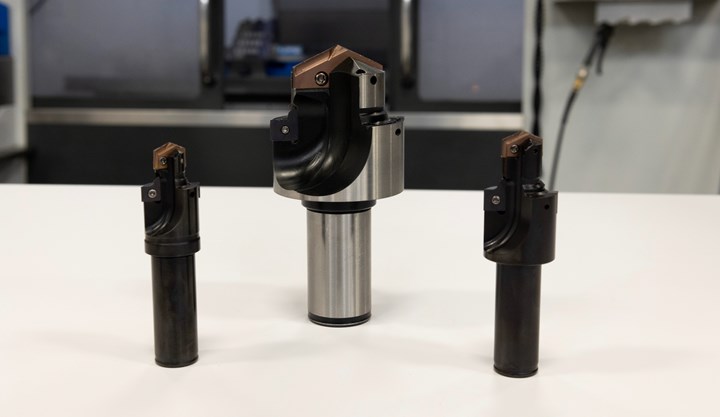
Indexable port machining tools can perform multiple operations in a single step while enabling shops to swap out worn inserts and return to production. (Photo Credit: Allied Machine and Engineering)
Another potential advantage of indexable port cutting tools is the ability to create custom tooling solutions. If an application requires a certain tolerance that a standard tool cannot provide or the standard tooling dimensional specs are not sufficient, custom tooling can be created. Whether it is a custom drill insert, custom port form insert, custom drill body or even all three, a special tool can be created to meet the requirements of the application such as a change in the spot face diameter. There are many instances in which a smaller spot face is required due to other constraining features on the workpiece or when a bigger spot face is needed in order to appropriately tighten the fitting. Custom, indexable tooling can help solve such challenging applications.
Indexable four-in-one tools for porting can also enable shops to cut at higher speeds or use port form inserts that can hold tighter tolerances, but, in addition, provide cost savings. It is also possible to use a port machining kit that includes a thread mill optimized for a given port requiring no special programming — another example of cost savings with these cutting tool solutions.
RELATED CONTENT
-
Turning to an Adhesive for Lathe Workholding
Adhesive cured by ultraviolet light is an option for securing parts for machining that could otherwise distort when traditional, mechanical clamping techniques are used.
-
Making Micro Threads
Production of micro threads can be challenging, but using the most suitable tools for a given application can simplify the task.
-
Skiving Long, Slender Parts with Tight Tolerances
Here's a look at one of the oldest and most efficient methods of screw machine production for parts that are long and slender, with close-diameter tolerances and finishes, or parts that require truly spherical radii.