C.O.R.E. Controller Technology Supports Machine Tool Connectivity
Appears in Print as: 'Controller Supports Machine Tool Connectivity'
The hardware/software architecture is designed to connect machine tools to open up possibilities for networking, controlling and monitoring the production process as well as process optimization.
#Industry40
Edited by Angela Osborne
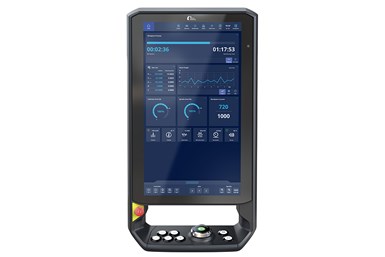
The C.O.R.E. panel has virtually no keys.
United Grinding’s C.O.R.E. (Customer Oriented Revolution) software and hardware architecture is designed to make machine tool connectivity possible, including networking, controlling and monitoring the production process as well as process optimization.
The 24" full HD multitouch display is said to offer intuitive operation, identifying the machine tools equipped with the C.O.R.E. technology. Navigation works like a smartphone in that users can “touch” and “swipe.” Customers can configure the user interface according to their individual requirements and arrange the most important functions and operating displays according to personal preferences — like the app overview on a smartphone home screen.
With this access system, which works via a personalized RFID chip, the individual user profile is automatically loaded, making it easier and more secure to log in and out of the machine. A roles profile is stored for each user, so users only see information relevant to them, thereby reducing complexity and helping to prevent errors.
The C.O.R.E. panel has virtually no keys. Instead there is a rotary switch for feed rate override, enabling the axes to be regulated with a simple turn, the company says. The uniform use of the panel across all brands also simplifies machine operation and makes training easier — anyone who knows how to operate one United Grinding machine can operate all of them.
The architecture also includes the C.O.R.E. OS, a full operating system which is installed on an industrial PC — the IPC. It serves as an IoT gateway and is home to all software applications. C.O.R.E. OS is also compatible with all CNC controls used at United Grinding.
Also, the technology can connect with third-party systems via implemented interfaces such as Umati. This opens up direct access to United Grinding’s Digital Solutions’ offerings on the machine — from remote service to the service monitor and production monitor.
RELATED CONTENT
-
5 Tips for Multichannel Programming
Programming for multitasking machines can be complex. Knowing several key points for making the process less challenging can save a programmer time as well as lessen confusion and the risk of error.
-
CNC Apps You Possibly Didn’t Know You Could Benefit From
Some software capabilities go underutilized. One machine tool builder’s CNC software includes lesser-known apps that shops can leverage to their advantage.
-
Compact Second-Op CNC Mill Gets Makeover
New control and programming capabilities make this small VMC well suited for second-op work or use as a standalone production milling machine.