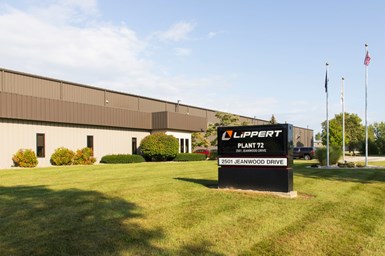
Plant 72, which is a 244,000-sq.-ft. building, houses an ecoat line, a powder coating line, a wet paint line and offers de-rusting and pickling as well as top coating and chemical agent resistant coatings (CARC). Photo Credit: Lippert
A business that is highly tuned in to market trends and its customers’ needs is one that is wise enough to adapt accordingly. Lippert, a metal fabrication company in Mishawaka, Indiana, that primarily serves the RV industry, is one of these companies. Its Plant 72, the company’s main coatings facility, has shifted from painting RV components to coating jobs outside the RV realm, including those in the automotive, military, agriculture, construction and aerospace industries. The company’s outreach over the last 4 years has not only diversified its customer base but has enabled it to become less affected by the volatile RV market.
“Instead of being a 95% RV company, which we were 6 or 7 years ago, we’re about 60% RV now,” says Joe Thompson, general manager at Lippert. “At this point, 40% of our market is outside of our core business.”
Featured Content
Opening doors to different industries has helped company management realize that Plant 72 offers coatings capabilities to many businesses that do not have access to paint facilities otherwise.
The EV customer attraction
Lippert has many coatings capabilities across its facilities for its internal RV component work. However, coatings are Plant 72’s main focus, and it is the only facility that pursues outside business. The company originally acquired it 10 years ago to help with capacity needs for its RV customers. But with the fluctuation of that specific industry, it has been able to move those in-house jobs out of Plant 72 and into its other buildings that have the capacity to support it.
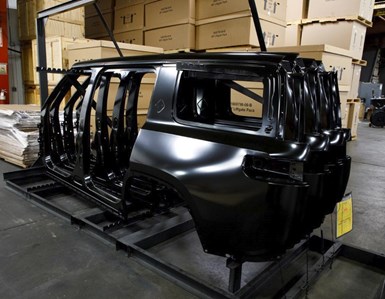
Plant 72, Lippert’s main coatings facility, has shifted from painting RV components to coating jobs outside the RV realm, including those in the automotive, military, agriculture, construction and aerospace industries. Photo Credit: Lippert
With this available capacity, the coatings plant, which completes a lot of Tier 2 and 3 jobs with quick turnaround (three to five business days), is especially attractive to the electric vehicle (EV) market. According to Thompson, the EV industry is racing to get these vehicles on the market as fast as possible.
“They need a facility like what we have (with a large ecoat capacity) to be able to do this,” he says. “Our customers can’t put up a facility overnight, but they are trying to get components out the door that fast. It is an interesting advantage for us.”
Plant 72, which is a 244,000-sq.-ft. building, houses an ecoat line, a powder coating line, a wet paint line and offers de-rusting and pickling as well as top coating and chemical agent resistant coatings (CARC). The facility has the capacity and equipment to perform multiple coating processes in a single building, which streamlines the production process.
Its ecoat line, affectionately called “El Chingón” by the plant’s team, is the largest non-captive ecoat system in North America, according to Thompson.
El Chingón
A Spanish term referring to something that has much power, Plant 72’s El Chingón is an indexing ecoat line that offers cathodic acrylic and cathodic epoxy coatings with an eight-stage zinc phosphate pretreatment cleaning system, which is U.S. Department of Defense-approved and meets military CARC specifications (T-TC-490E Type 1).
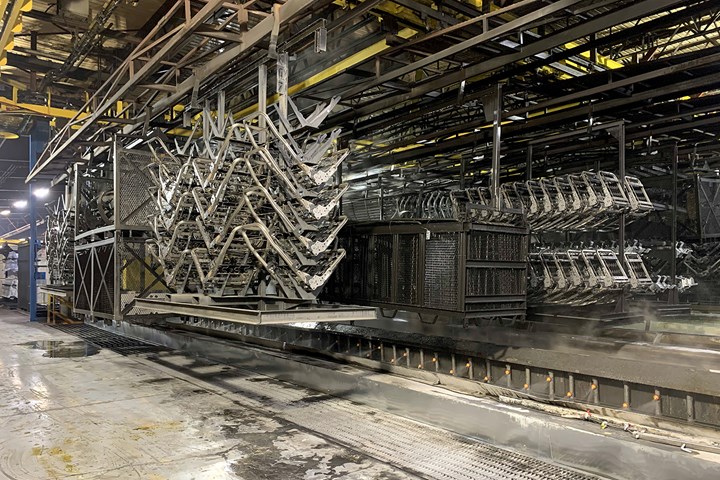
Plant 72’s “El Chingon,” the company’s huge ecoat line, is said to be the largest non-captive ecoat line in North America, with dimensions at 50' long x 9' deep x 63" wide. The equipment offers an eight-stage zinc phosphate pre-treatment cleaning system as well. Photo credit: Products Finishing
Thompson describes the machine’s specs. “The load bars that are carried through the index can handle 6,000-lb. max part weight at one time or 2,000 sq. ft. of product, whichever maxes out first,” he says. “Each of the eight pretreat tanks are 50 ft. long, 10 ft. deep and 65.5 inches wide. The tanks can hold up to 30,000 gallons of product.”
The cathodic epoxy offered has 1,000-plus hours of salt spray resistance. The cathodic acrylic can withstand up to 750 hours of salt spray resistance and UV protection. Its pretreatment and epoxy ecoat meet most automotive and military specifications.
Powder coating and more
Plant 72’s powder coating line is a standard system with manual powder guns that can do quick color changes with multiple colors available. The line, which also has a zirconium pretreatment system that stands in front of it, is 15 ft. long by 3 ft. wide by 6 ft. tall.
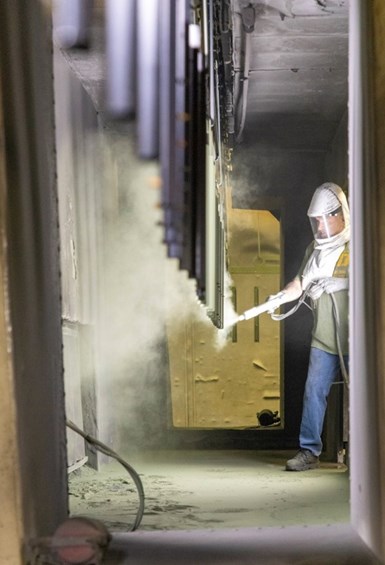
Lippert offer a variety of powder coating color options and can accommodate products up to 10' long, 5' deep and 2' wide. It also uses a NT-1, five-stage cleaning process on all its products. Photo Credit: Lippert
Although the capacity of this powder coating line does not match the large capacity of the plant’s ecoat line, Thompson says Lippert has plans to build a powder coating facility nearby that matches it.
Fortunately, the company owns nine powder coating facilities all within the vicinity of Plant 72 that can match the capacity of its ecoat line. Therefore, when the demand arises for a large part to be powder coated, the plant will ship the work to one of these other facilities to finish the job.
All coated parts are force cured at the plant. “We have an enormous oven for ecoat, and other ovens for the powder coat and wet coat processes,” Thompson explains.
Other capabilities that the facility boasts include a wet coat line — which sprays wet paint that is 20 ft. long by 5 ft. wide by 10 ft. tall — light assembly, packaging and shipping.
Boxing and blasting
Because Lippert understands that value-added opportunities are becoming increasingly critical to stay competitive, the company is doing light assembly as well as boxing and labeling of service parts for its automotive and military customers.
“This (in-house shipping operation) has been a growing market of ours,” Thompson explains. “Most manufacturing facilities don’t want to shut down their coating lines for their service parts. So, we’ve become a one-stop shop here where we box them up, and they’re ready to go wherever the need is.”
Bringing the packaging and labeling process in house is one example of how Plant 72 is constantly devising paths to improvement. Staying abreast of the latest equipment or processes in the industry is another way. When management realized that implementing a blasting system would be advantageous for its customers, it began planning for the installation of a media blasting booth, which is currently underway. The blast booth matches the plant’s ecoat capacities; it stands at 60 ft. long by 10 ft. wide by 10 ft. tall.
Predictive maintenance
With a large, 30-year-old machine like El Chingon, Plant 72 has learned that nonstop maintenance of this equipment is the key necessity to keeping it and the business running smoothly.
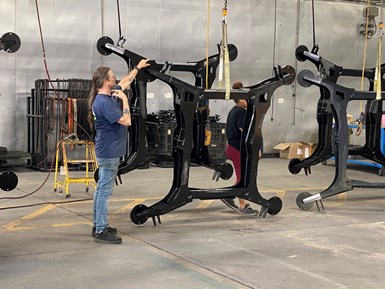
All coated parts are force cured at the plant. It has an enormous oven for ecoat, and other ovens for the powder coat and wet coat processes. Photo Credit: Products Finishing
“To be able to maintain that and stay in front of it has been a huge feat,” Thompson says. “We cannot afford to have our equipment go down, so we stay on top of that game.” He adds that even a little downtime is problematic because the ecoat line produces so much work, and it is a costly investment to keep it running.
However, Thompson gives credit to the predictive maintenance systems that the company has been putting in place. Also, the facility’s attentive team changes out parts before they fail instead of after, when it is too late.
On the horizon
While Lippert is busy predicting maintenance for its equipment, its management is also doing its best to predict the future market trends that will affect its business.
Although the RV market benefited from the COVID pandemic where it saw a boom in sales, 2023 was a hard year for the industry. It faced a heavy slowdown then, but according to Thompson, the company believes it has seen the bottom of it. “It is starting to pull out, but I don’t think this year we will hit the numbers we did during COVID — it was tremendous,” he says.
Like the RV industry, the marine market (of which Lippert is an OEM supplier) boomed during the pandemic but is slowly bouncing back, Thompson says. With spring around the corner, the company is prepared for business to pick up in that area.
With demand for coatings in many different markets, Lippert has plans to expand its coatings presence, especially in the south. Thompson says the company would like to open a new facility there with ecoat and similar capabilities and capacities to what Plant 72 offers.
“We’ve figured out how to be successful in coatings, and how to make it a financially viable business unit, and also partner with people with that need which opens doors for us across the rest of our business,” he explains.
RELATED CONTENT
-
How Small Machine Shops Can Fight Supply Chain Problems
Supply chain disruptions are still presenting challenges in manufacturing. This article examines the effects on aerospace, automotive and medical industries. It also covers ways that machine shops can be successful securing work despite the challenges created by the supply chain.
-
In-Machine Probing Possibilities for VTLs
A manufacturer of vertical turning centers uses a “push/pull” optoelectronic probe with custom bracket to enable its machines to perform effective, in-process measurement of shafts and related automotive components.
-
A Race to the Machined Part (Surface) Finish
To improve component finish as well as engine and gearbox performance for its customers, this racing motorcycle rebuild company uses a super-finishing process for gears and related components which is more commonly used for aerospace and jewelry applications.