Automation, much like Henry Ford’s assembly line, is transforming the manufacturing workplace. Therefore, it is in a company’s best interest to determine how to leverage this movement. For Saint-Gobain Abrasives, it is two-fold: How can we introduce more automation into our factories to create a better worker experience and increase throughput? And, even more important to industry, how can our product portfolio evolve to better complement the expanding capabilities of automation? We are working hard every day in our Norton Abrasive Process Solutions (APS) automation lab to show customers how their grinding and polishing operations can be automated.
Advancements in automation address many of the most pressing demands in the industrial manufacturing workplace today. Whether you are struggling to find enough workers to fill your factory, looking to reduce ergonomic-related injuries, facing stricter workplace safety regulations or needing to increase factory capacity and throughput, automation is likely to be an important part of the solution.
Featured Content
Increasingly, we are seeing customers looking to automate their most repetitive and often dirtiest jobs to combat these labor issues. Robots and other automation tools show up to work every day and are exceptionally productive in repetitive tasks. Furthermore, workers who tend automation cells rather than perform manual operations are more likely to stay in their role longer. Simply put, automation means less worker turnover and fewer ergonomic- and fatigue-related injuries — all of which adds up to better throughput.
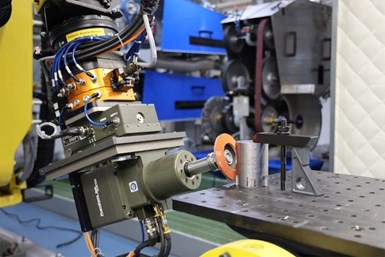
A robot may take tools out of workers’ hands, but that robot must also be tended. With advancements in intuitive interfaces to control robots, these workers can be trained to do so. Also, once employees have been trained, employers will often deploy them in other areas of the factory. Photo Credit: Norton | Saint-Gobain Abrasives
As great as automation can be, the idea of automation is often met with resistance from workers and organizations fearing that robots will replace jobs previously completed by humans. I would like to take a few moments to address those fears.
First, a robot may take tools out of workers’ hands, but that robot must also be tended. With advancements in intuitive interfaces to control robots, who is better to train and oversee the robot than operators who have already done the job and know what quality parts look like?
Second, dedicated and reliable employees have become harder and harder to find in today’s labor market. Once employees have been trained, employers will often gladly deploy them in other areas of the factory.
Have you thought about how automation opens up opportunities for workers? Consider a labor-intensive grinding operation where an operator presses heavy parts against a grinding wheel for 8-10 hours per day. Historically, this has been a job for younger and physically stronger individuals. However, once this operation is automated, the robot manipulates the heavy parts, removing manual work, and changing and elevating the operator’s role to oversee and inspect the process. Now this operation can be completed by operators of all ages and all levels of physical strength, thus creating opportunities for a much broader labor pool.
In the grinding and polishing world, which is where I spend all my time, the challenge has always been giving the robot that “human touch” and “human eye.” Advancements in what is referred to as compliance in the automation world enables a robot to maintain a specific amount of force in a grinding or polishing application, mimicking “human touch.” The “human eye” component is also being addressed with integrated vision systems that are simplifying both the pick-and-place and final inspection processes. Whatever automation challenges exist in your industry, there is a good chance that those obstacles are also being overcome.
Even if you considered automation in the past, and it did not appear to be a viable option, I encourage you to take another look to see how advancements in automation may now offer you a solution.
Norton | Saint-Gobain Abrasives | nortonabrasives.com/en-us
About the Author
Tony Landes has been with Norton | Saint-Gobain Abrasives for 29 years where he has held several engineering and management roles, including his most recent position as manager of the Abrasive Process Solutions program. Tony has two degrees from Tarleton State University (Stephenville, Texas) including a bachelor’s degree in industrial technology and a master’s degree in business administration.
RELATED CONTENT
-
Job Shop Discovers and Fills a Fishing Need
The promise of a product line for improved mounting of electronic fish finders led this Missouri job shop to an automated turning process.
-
The Promise of a New Access-to-Capital Model
A free online loan prequalification tool currently offered in Colorado with the potential for introduction to other U.S. markets can enable manufacturers to more easily finance new technologies including automation equipment.
-
Machine-Tending Cobot Fills Night Shift
A collaborative robot helped this shop run a machine tool 24/7 when hiring someone for a third shift didn’t seem to be an option.