Adding Value, Reducing Cost with Inverted Vertical Turning Centers
Appears in Print as: 'Adding Value, Reducing Cost'
Inverted vertical turning centers find a home in an automotive stamping house.
#horizontal-and-vertical-lathes
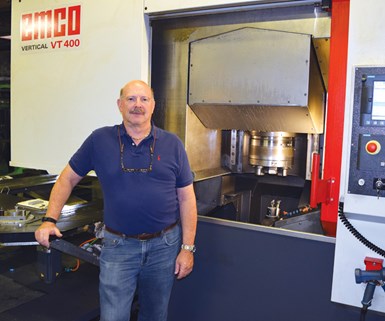
Philip Frankle, president and CEO of Stamtex, has integrated inverted vertical turning machines into his high-volume fabrication shop. The machines have allowed the shop to bring work in-house that was once contracted.
This is not a story about another big plant machining transmission parts. Rather, it is a story about a family-owned firm using self-contained inverted vertical turning centers to meet quality and volume demands from automotive Tier-One suppliers in a hot market of primarily brackets and flanges for automobile exhaust systems.
Stamtex (Niles, Ohio), a stamping shop established in 1921, has always supplied to the auto industry, including every brand of automobile. The shop’s production is currently about 85-percent automotive work, including aftermarket. That’s about 2,500 part numbers. It is the No. 2 supplier of heavy exhaust stampings in the country, according to the company.
Featured Content
High Volume
The volumes of parts flowing through the shop are huge, and the consequences for downtime are equally significant. So, like many family-owned shops, Stamtex works to avoid downtime through careful planning. And it works to add value to the product it delivers. For stamping and metalworking shops, that means doing more work in-house where the inventory control and quality can be improved and critical ISO standards are maintained.
Rapid response to automotive demands is one of the company’s core values. This means it’s imperative to create in-house all the tooling necessary to produce high quality parts, which the company is doing. It operates high-end EDM machines to craft its stamping dies and produces 95 percent of its die sets in-house.
Avoiding outside production steps, and adding value to the parts it ships by adding features and fasteners, is also critical for the company, which gives it an edge over the competition.
Turning Upside Down
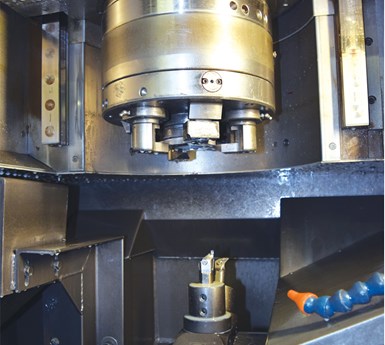
The inverted vertical turning center uses a main spindle for machining and uses it as a loader and unloader, as well.
To reach these goals, Stamtex uses two inverted vertical turning centers that are installed on the production floor next to the press lines.
The company produces millions of heavy flanges for a car’s exhaust system yearly. Some of these parts include a groove on one side in which a sealing gasket is set. The gasket permits a tight connection, preventing exhaust gases from escaping. Both Ford and General Motors use this system.
Previously, this groove feature had been done by an outside vendor on a CNC lathe, one part at a time, with an operator handling each part, followed by a cleaning operation. But as with almost any outside supplier, it was an added cost to the part. Contracting work added time and handling, and it interrupted what could be a smooth production flow in a single location.
So Stamtex President/CEO Philip Frankle decided to bring the operation in-house. He implemented an inverted vertical turning center into the process because of the types of operations—turning, grooving and tapping—the company would perform on mainly flat parts, such as flanges, hubs and brackets.
Calling Motch & Eichele (Cuyahoga, Ohio), an EMCO master distributor, Mr. Frankle asked for suggestions for solutions. M&E brought in EMCO to present a solution to Stamtex, whose fundamental needs included the ability to perform operations on datum A (flat surface). Parts had to be loaded and machined on datum A and either returned to the conveyor or placed in an exit chute from the machining area to the operator. There, the part surface and the depth of the groove to be machined are checked.
After careful consideration, Stamtex invested in an EMCO VT 400 inverted vertical turning center. The machine had the capacity and power to handle tough stainless steel parts and offered the flexibility to handle what might come in the future. The turning center has a conveyor loop supplying the part pick-up station that would permit unmanned operation for an extended period. Other machines did not offer this capability as standard.
Self-Contained
Because the VT 400, with its integrated pick-up system, self-loads workpieces, it saves Stamtex the costs and programming time related to external automation. This loading and unloading design allows for fast part-to-part times of 13 seconds with workpieces weighing up to 88 pounds. Compared with other traditional methods using gantries or robotics, this design is about 300 percent faster, according to EMCO.
The EMCO conveyor brings the parts to and from a common loading and unloading location outside the machining area to the machine spindle for pick up.
“The machines provide us the ability to pick up the part the way it naturally orients, which is datum A down, and as it is machined from below, the chips and coolant fall away and give a clean part coming off the conveyor, saving a wash operation,” Mr. Frankle says.
The first VT 400 was installed at Stamtex five years ago; a second came three years ago. The controls for the machines were familiar to the company as they are similar to the CNC in the die shop, so the learning curve was short and simple. The turning center typically is controlled by the Sinumerik 8280 from Siemens with an option for Siemens ShopTurn conversational programming and the FANUC Oi Control.
The EMCO turning center consists of the workpiece load and unload system and the vertical spindle with 12-position tool turret below it. The machine can store parts on its feed side in a buffer loop. The parts, placed in carriers on the loop, are conveyed to a pick-up station where the three-jaw chuck grips and clamps the plate and moves it into the machine to the main spindle. The pick-up system removes the need for additional loading equipment, making it simple to handle a range of different parts if production needs change.
Double Duty
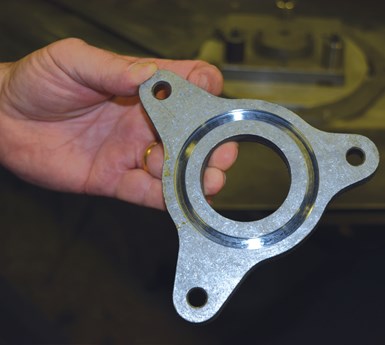
Machined on Stamtex’s vertical turning center, the groove on this flange is high tolerance.
A pneumatic workpiece equipment monitoring device checks for precise workpiece clamping and alignment in the chuck. All machining movements on the X and Z axis are actuated through the main spindle.
The design of the work area maximizes efficiency. For the flange part at Stamtex, the VT 400s are tooled with only two carbide insert tools—one for roughing and one for finishing the groove. The tools work from beneath the surface to be grooved, allowing chips and coolant to fall away into the high-capacity chip conveyor for disposal outside the machine. The machining cycle is only 15 seconds, with the first tool taking a plunge cut, followed by the finish cut in the 409 stainless material.
The vertical turning center also includes an easy-to-use tool breakage monitoring system with automatic adjustment of the monitoring parameters to ensure process integrity within the machining cycle.
After turning, the three-jaw chuck feeds the workpiece to the discharge position. In combination with the feeder and automated sequences during the machining process, this allows unmanned operation. A skilled setup person controls and monitors machining and also does tool changes.
The VT 400s easily keep up with the press volumes with unmanned, highly consistent machining, and part handling has been dramatically reduced. Performing these grooving operations in-house means the company controls the quality of the part, and can ensure its customers of the processes’ integrity.
These machines make sense for Stamtex. They offer a 320-mm maximum turning diameter, 200-mm part length and 4,000-rpm spindle speed with 60 Nm of torque. The machine has the capacity to handle customer part sizes and designs as they evolve. It is able to process tough steel parts quickly and consistently in high volumes, providing plenty of easy access for tool change and part loading. The 12-position tool turret includes an 8.5-kW drive of each tool with 40 Nm of torque.
According to an EMCO engineer, “The VT400 has the flexibility to perform multiple machine operations with short setup and retooling times. This reduces waiting times, resulting in a more productive machining environment. We optimize production processes to reduce chip-to-chip times, supporting complete, efficient part machining for simple or complex workpieces.”
Both vertical turning centers at Stamtex are the same to the last detail, and they are programmed the same, providing the shop the ability to move jobs where needed, when needed. Each machine has an operator, permitting the company to keep both machines’ uptime maximized. “Our customers don’t want to hear ‘we can’t,’ so I back up everything,” Mr. Frankle says. The machines process about 10 percent of the shop’s total volume.
The productivity and quality benefits are clear to Stamtex. Once the company had optimized the process, it was able to improve productivity on the flange part by about 400 percent. Uptime has been good, and its customers receive high quality parts on time. Mr. Frankle says if the company requires additional capacity, he will shop for a third EMCO VT.
RELATED CONTENT
-
Tooling Up for Micromachining
Choosing the right tools and matching them to the correct operations and process techniques for micromachining applications is critical to success in this burgeoning market.
-
Understanding – and Machining – Ultra-Clean Steel
Using the strongest steel available to create critical automotive powertrain components is necessary and in demand. Understanding how to properly machine ultra-clean steel and executing these techniques will enable cost-efficient and consistent part production.
-
Using Grinding Instead of Turning in Series Production
By grinding the entire workpiece contour in a single operation, the Grindstar can produce large batch sizes economically, making it an alternative to turning for the automotive industry.