Acu-Rite TurnPwr Control Enables Manual, Automated Lathe Operations
Appears in Print as: 'Lathe Control Enables Manual, Automated Operations'
It enables users to maximize throughput by significantly reducing setup time, scrap and other nonproductive operations, thereby increasing efficiency, productivity and profitability.
Edited by Angela Osborne
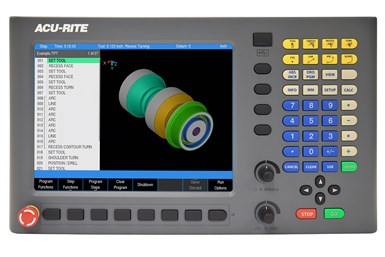
Acu-Rite TurnPwr Control
Acu-Rite’s TurnPwr control is a workshop-oriented turning control for lathes that enables users to program conventional machining operations right at the machine in an intuitive conversational programming language. It is designed for lathes with up to two axes.
TurnPwr was developed to offer lathe machinists both manual and automated operation where useful or needed. It enables users to maximize throughput by significantly reducing setup time, scrap and other nonproductive operations, thereby increasing efficiency, productivity and profitability.
The company says that the Acu-Rite conversational programming format for controls is a user-friendly method of writing part programs and included in the TurnPwr. However, G-code (ISO) programming can also be used and basic editing of G-code programs is also possible.
The control features a 12.1" high-resolution display boasting a screen layout that is clearly arranged. Preview graphics in the editor illustrate the individual machining steps for programming the contour as well as corresponding tool path generated, using only dimensions pulled from a production drawing. It also accepts DXF files.
TurnPwr is a closed-loop system with positioning feedback provided by rotary encoders inside the motor assemblies. When fitted with the (optional) Acu-Rite precision glass scales (1 µm/0.00005" resolution), TurnPwr also includes Position-Trac, an advanced feature that enables the user to easily, quickly and accurately reestablish workpiece zero after shutting down or power loss.
RELATED CONTENT
-
A Fitting Machining Process
Diversified Fittings has turned to twin-turret/twin-spindle equipment and machine monitoring to become more efficient producing hydraulic fittings and adaptors.
-
Okuma’s OSP Control is 50 Years Old
In 1963, Okuma introduced its first CNC the OSP. OSP stands for Okuma sampling path, which emphasized the innovation of creating a digital representation of a machine tool’s cutting path.
-
Manufacturing Automation Beyond Robots at PMTS
A variety of automated machining and manufacturing processes — including, but not limited to, robotics — that can enable shops to become more efficient were on display at the recent Precision Machining Technology Show.