WORKHOLDING & HANDLING
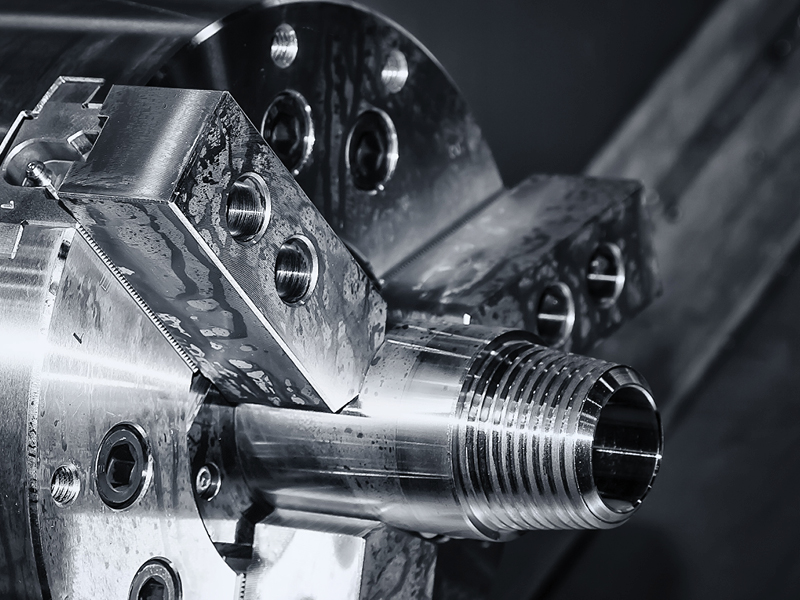
Workholding devices such as collets, chucks, live centers, guide bushings and steady rests can optimize turning and milling processes while robots, gantry loaders and pallet changers can automated workpiece handling.
Narrow by Workholding & Handling Product Category
-
Workholding
- Actuators, Hydraulic & Pneumatic
- All Other Workpiece Handling, Loading & Feeding Equipment not specified
- Angle & Sub Plates
- Arbors, Expandable Workholding
- Centers, Live & Other
- Chuck Jaws & Collets
- Chucks, Collet Type (for Workholding)
- Chucks, Diaphragm
- Chucks, Gear
- Chucks, Index
- Chucks, Jaw Type
- Chucks, Magnetic
- Chucks, Power
- Chucks, Precision
- Chucks, Self-Contained
- Chucks, Special
- Chucks, Vacuum
- Clamps & Fixturing Devices
- Collets for Workholding
- Dividing & Indexing Heads
- Fixturing Systems
- Guide Bushings (for Swiss Lathes)
- Indexers & Rotary Tables
- Mandrels
- Pedestal Type Fixtures & Tombstone Blocks
- Steady Rests
- Vises & Vise Jaws
- Workholding, Custom
FAQ: Workholding & Handling
Are there tools to make programming robots easier?
Those with no robot experience might be apprehensive about programming them and connecting them to a machine tool. However, robot manufacturers continue to develop technology to streamline and simplify this, and the new Quick and Simple Startup of Robotization (QSSR) G-code feature from FANUC America is one example.
The QSSR G-code feature enables machine shop personnel to program FANUC robots through a FANUC CNC using the ISO-standard G-code format. It is designed for those who are familiar with G-code programming, but not robot programming languages, making additional training for robot programming unnecessary.
For robot programming, an operator selects the desired robot coordinate system from the CNC and the robot can be moved to specific locations using the CNC’s manual pulse generator (MPG). This reduces the reliance on a separate teach pendant for the robot. The movement of the robot is learned and a robot G-code program automatically created. This program is then stored on a dedicated program path for the robot.
(Source: Program a Robot with your Machine’s CNC)
What are the benefits of adding robots to a machining process?
Here is a list of the most tangible benefits for a machining process:
Process Control. A properly designed automated process ensures that things happen when they are supposed to and how they are supposed to. The result of this process control is reduced scrap, higher quality and more throughput resulting in higher customer satisfaction.
Better Machine Usage. A machine that is not running generates no income for the shop. Typical machine usage for a manual machining process is 65 percent. For a comparable automated process, this number is more than 90 percent. Better machine tool usage results in a faster return on investment for the machine tool.
Higher Production Capacity. Robotic automation can allow the opportunity to run untended operations. This provides additional production increases to those because of process control and machine usage.
Better Use of Labor. The most flexible and most valuable resource in any company is its people. A better use of that resource is not necessarily for machine tending, but for machine setup and other operations that may not be suitable to automation, such as part staging, secondary operations, quality control functions, packaging, and so on.
Flexibility. Quick response by being better able to respond to changing production requirements creates the leaner, more agile and more efficient operation necessary for today’s market.
(Source: Robotic Automation's Challenges, Solutions and Benefits)
Get Listed!
Thousands of people visit this Supplier Guide every day to source equipment and materials. Get in front of them with a free company profile.